InteWall
InteWall is a pre-panelised internal partition system designed to increase onsite efficiency and reduce waste. Designed for manual movement on site, InteWall is quick and simple to install, bringing certainty of system performance, site productivity improvements and particularly suitable for use in high rise residential and multi occupancy buildings.
Key Metrics:
- Design time saving: 32 hours per floor reduced to 2 for whole building when using KOPE.
- Standardization rate improvements: up to 12% increase in standardized panel use, improving project viability.
- Reduced on site waste: recorded 92% reduction of onsite waste compared to traditional install.
The challenge
Identifying which projects were suitable for InteWall was taking considerable effort and relied on a skilled designer with extensive system understanding to place panels optimally. It took approximately 4 days per floor to digitally place and configure InteWall panels on a project.
Of the 100s of possible layout solutions, only a handful could be tested given the time restraints, so best judgement had to be made. Once designed, the number of bespoke panel requirements could be calculated and a project’s suitability determined. If too many bespoke panels are needed the manufacturing costs end up too high to be feasible and the 4 days of design time is wasted. Saint-Gobain approached KOPE to support their InteWall digital offering goals, and show we could improve the outcome and process.
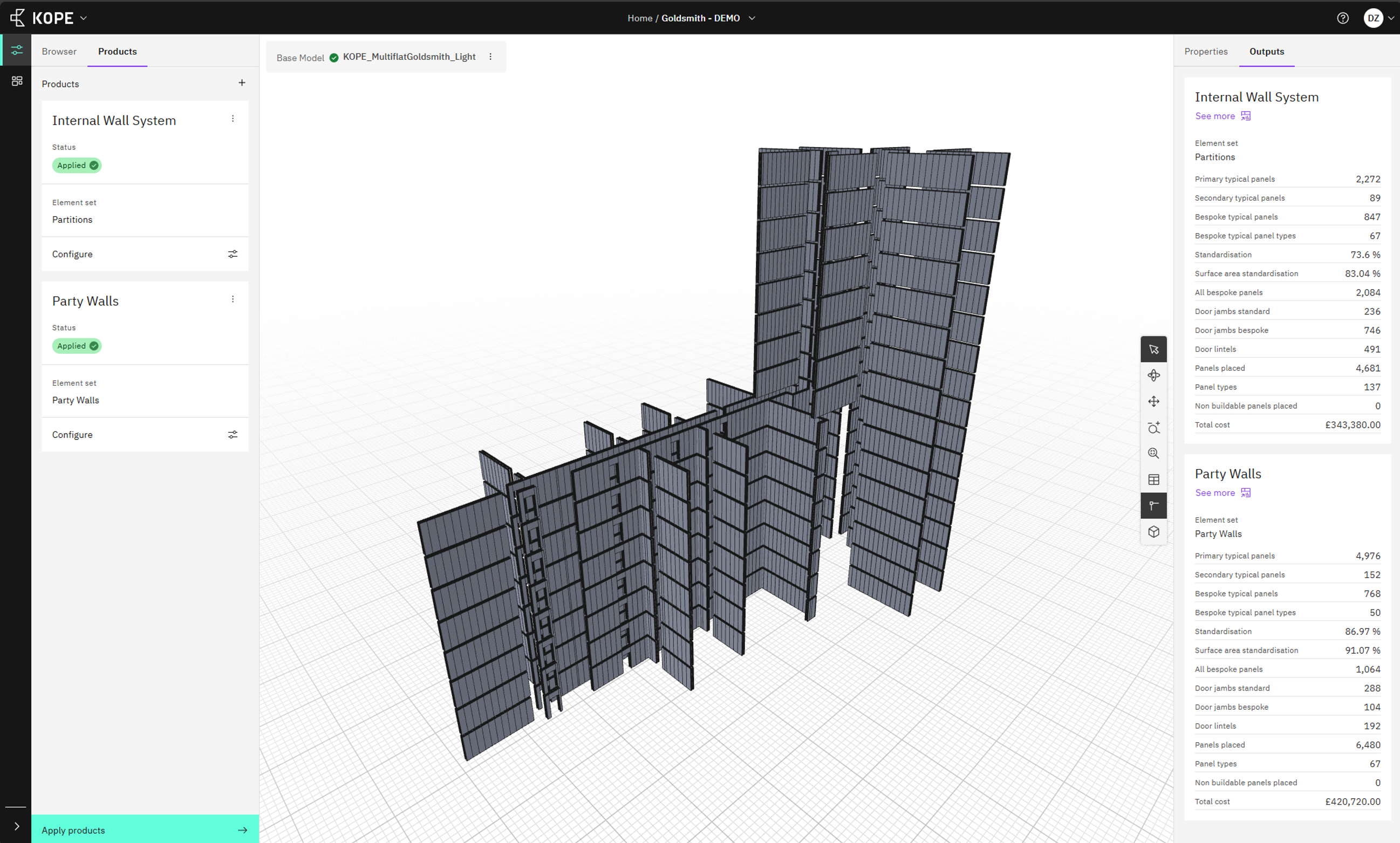
The System
Maximising the use of InteWall 600mm wide panels is the core of its system logic. This significantly reduces material waste, simplifies the install process and reduces the manufacturing demand for bespoke panel sizes.
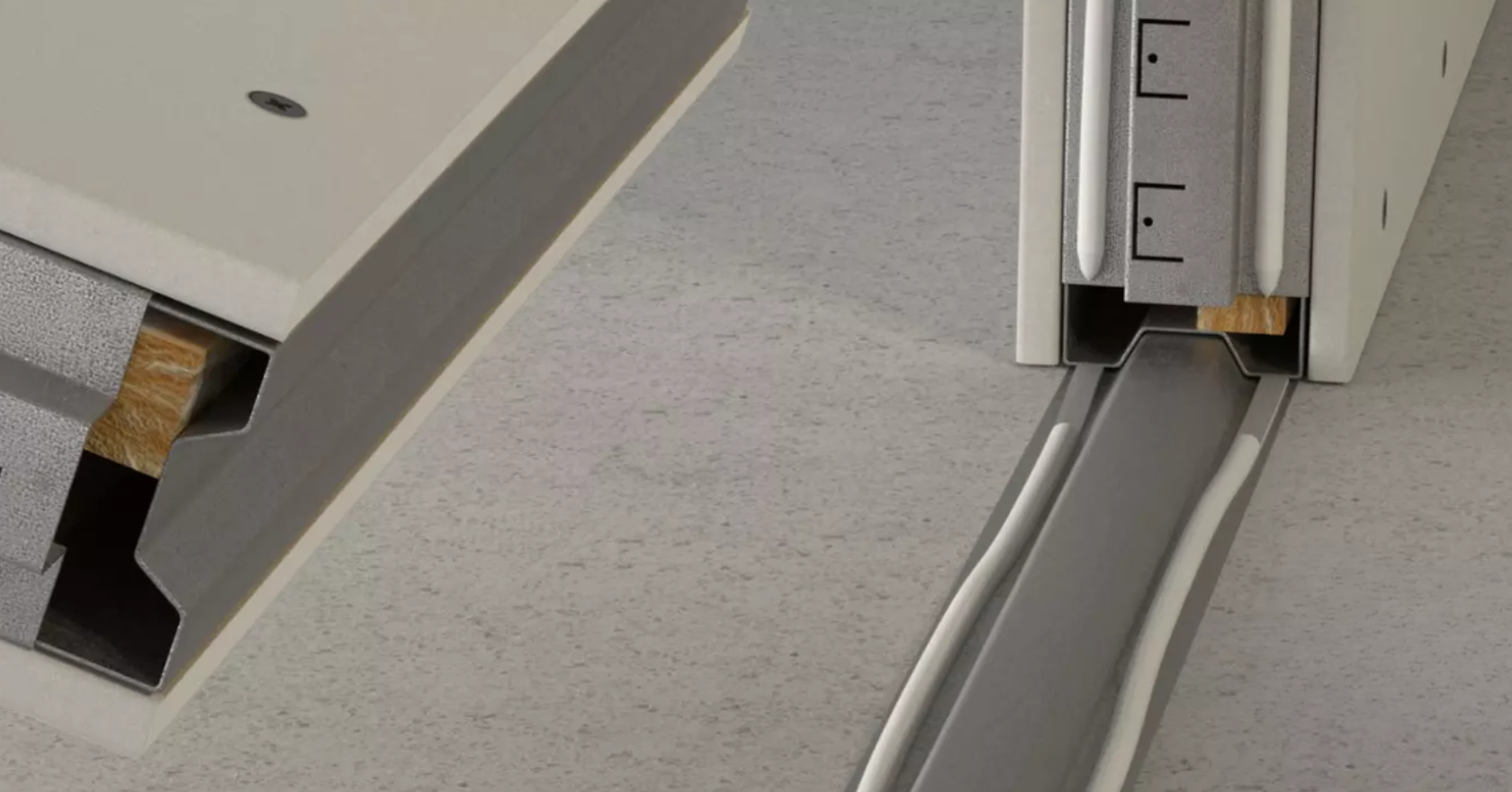
Using KOPE’s Kit of Parts logic, InteWall panels are applied across a project to identify the locations of standard panels and the required bespoke panels needed to complete the design. Within 15 minutes, the InteWall team now have a manufacturable panel solution for the entire project, not just a single floor. A huge time saving compared to the 32 hours previously taken.
.png)
However, as this scheme had been designed with a traditional partition system in mind, this “as-designed” base design often results in a low standardisation rate, and requires significant bespoke component manufacturing.
Opening position variation
As part of InteWall’s manual design process, designers often make small adjustments to door opening positions to reduce the number of bespoke panels needed on a project.
KOPE implemented a “Flex Openings” strategy to capturing this logic, allowing the InteWall activity to adjust opening positions up to 100mm from it’s original position for the purpose of reducing the number of bespoke panels.
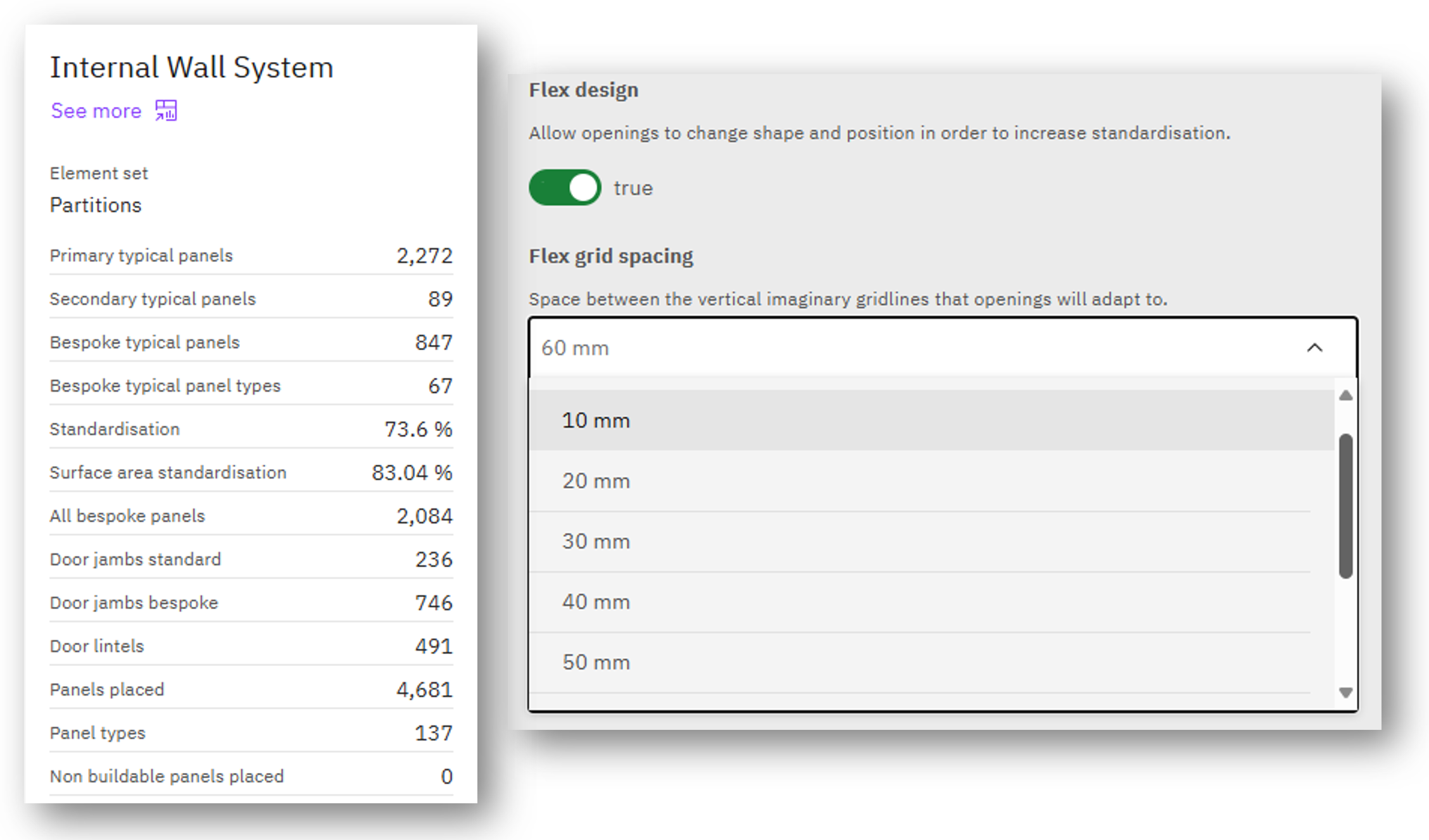
This flexibility regularly saw up to an 8% increase in standardisation across a project (typically over 1000 more standard panels), and often pushed a project into the 'viable scheme' category compared to the as-designed solution.
Optimisation engine
Not all bespoke panels are created equal though. Unless a project team uses InteWall’s standard panel sizing from design inception (and those teams see huge project savings), all projects have some bespoke panel requirements.
100 bespoke panels of the same size is significantly better than having 100 bespoke panels each with a unique size. Where the initial placement of standard panels are on a wall has the biggest impact on the size/amount of bespoke panels, and the more of these that can be the same, the better for the project.
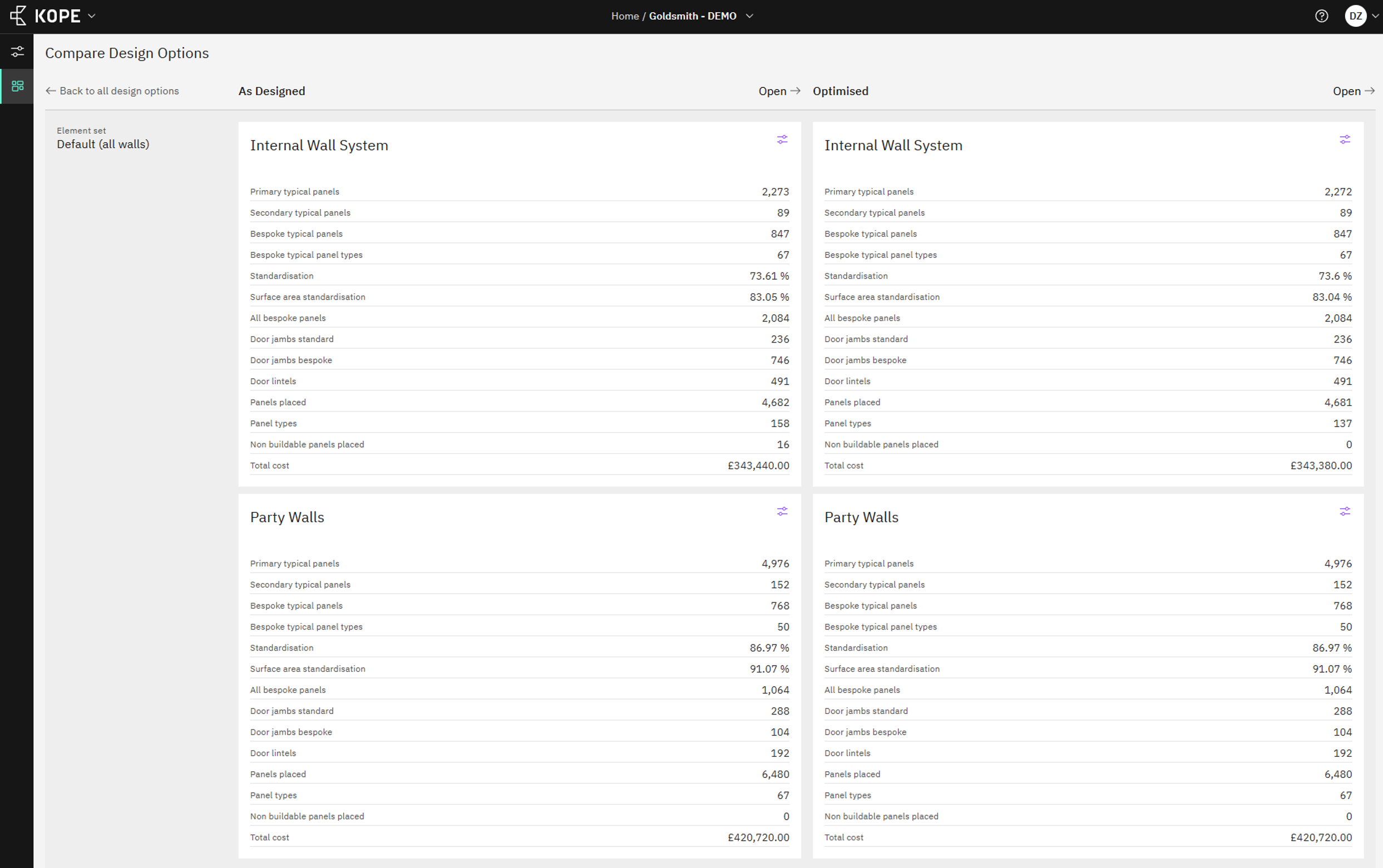
Given InteWall projects are high-rise residential projects, there are typically 1000s of walls that need to be taken into consideration. Combined with competing metrics such with door opening positions, panel counts, waste reduction etc. this is a very difficult challenge. To know which configuration input will impact each outcome optimally, and which combination gives the best overall value across the competing metrics, is nearly impossible to achieve manually.
.png)
KOPE’s optimisation engine allows the team to set the configuration ranges allowed for a project, weighing the desired metrics against one another, running scenarios and refining 100s to 1000s of possible combinations. All with the aim of finding the most suitable outcome.
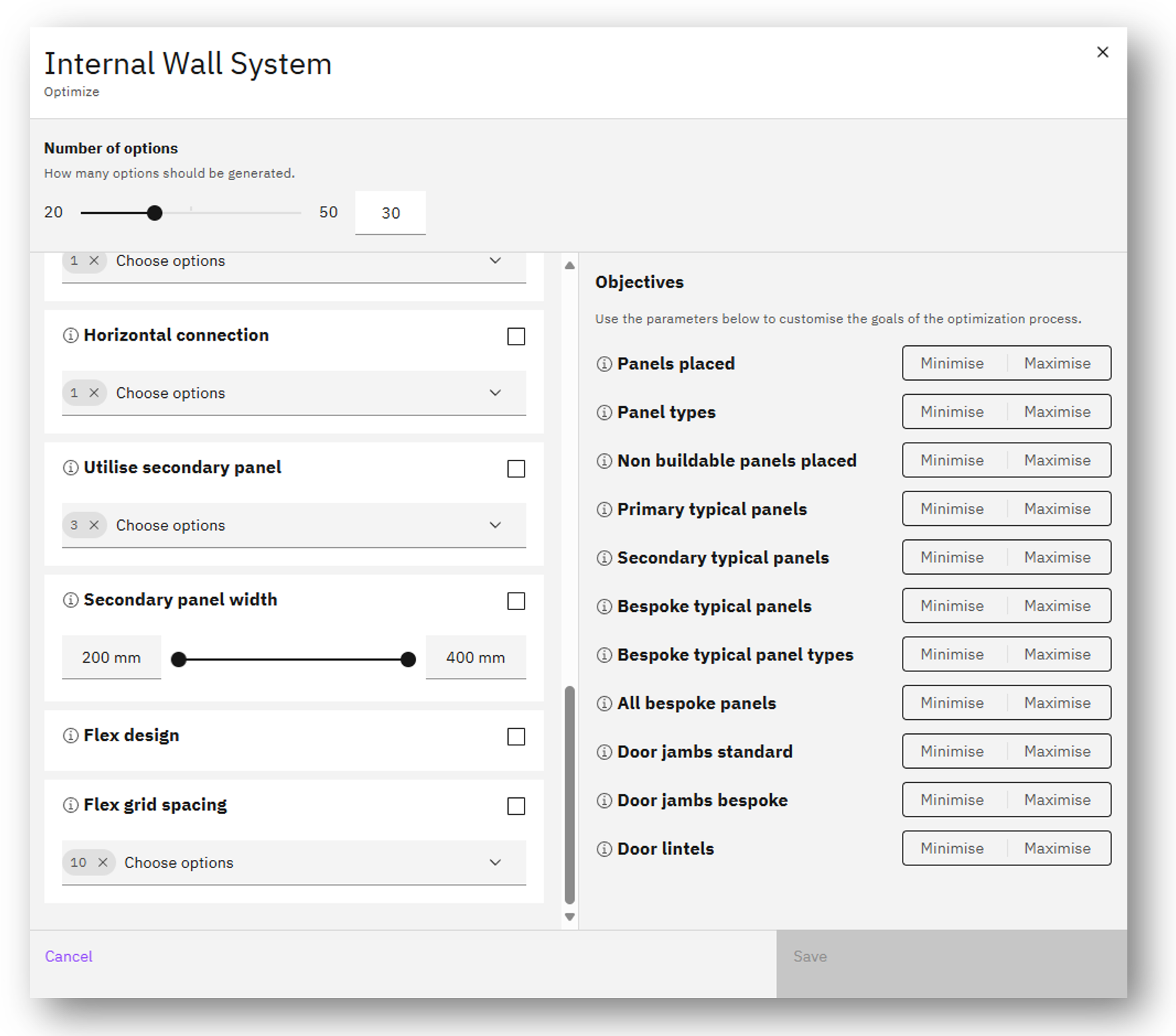
Compared to manual inputs, this has resulted in a further 18% improvement in standardisation.
The real world impact here is supporting many more projects being viable, enabling the InteWall system to be used more widely, with less risk and more cost insight.
“KOPE fundamentally enables our digital product offering for InteWall.” – Tom Cox, Construction Solutions Director, Saint Gobain
InteWall on KOPE
From taking 4 days to design a single floor, to generating an entire building solution in minutes. Along with testing 100s of optimised alternatives in under an hour, InteWall is able to deliver more projects, of larger size, and more suited to the InteWall solution. A clear example of KOPE's mission statement in action. To enable more prefabricated products to integrate with projects, at any stage of design.
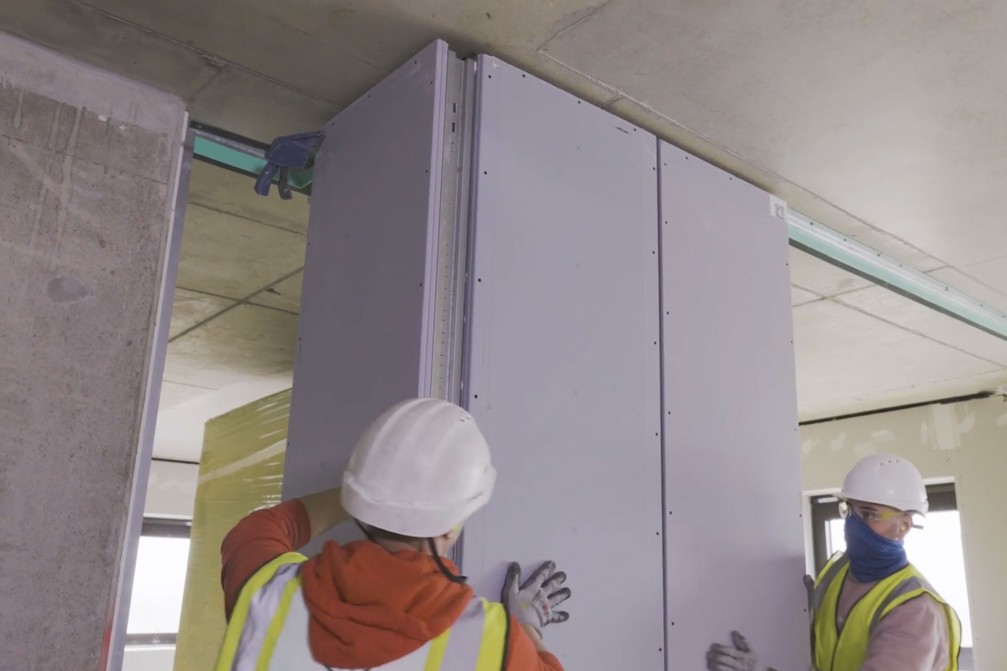
If you have a design process that could benefit from automated product placement, that has multiple conflicting metrics that need to be optimised, reach out to KOPE.