10 years!
Now that’s nothing in comparison to some of the people I have had the pleasure of rubbing shoulders with but I thought to take a moment to reflect on what I’ve learned and continue to see across our industry.
I've dedicated the past decade of my career to the construction industry, specifically construction software. Throughout this time, I've witnessed remarkable technological advancements aimed at revolutionizing the way we design, build, and manage projects. From sophisticated project management tools and Building Information Modelling (BIM) to advanced scheduling and cost estimation software, the potential for efficiency and productivity gains is immense.
I've also had the distinct pleasure of collaborating with some of the most intelligent and experienced professionals across the globe. Despite the industry's seemingly slow adoption of new technologies, these interactions have showcased the incredible depth of knowledge and expertise within our field. From seasoned project managers and visionary architects to innovative software developers and skilled tradespeople, everyone has provided invaluable insights that have enriched my understanding and driven my passion for advancing construction technology, my career has been shaped by each of them.
Despite incredible innovations, I've observed a consistent lag in the industry's adoption of new technologies. Several factors contribute to this slow implementation:
- Resistance to Change: Many construction companies have long-standing processes and are hesitant to disrupt their workflow with new technology. This resistance often stems from a fear of the unknown or a comfort with traditional methods that have worked in the past.
- Training and Adaptation: Implementing new software requires training and a period of adjustment. The construction industry, known for its tight schedules and budget constraints, often finds it challenging to allocate time and resources for comprehensive training programs.
- Cost Concerns: The initial investment in new software and technology can be significant. Many companies, particularly smaller firms, are wary of these upfront costs, even when the long-term benefits are evident.
- Integration Issues: Construction projects involve multiple stakeholders, including contractors, subcontractors, architects, and engineers, each potentially using different systems. Integrating new software with existing tools and ensuring seamless communication between all parties can be a daunting task.
- Lack of Customization: Off-the-shelf software solutions may not meet the specific needs of every construction project or company. Customizing these tools to fit unique requirements can be time-consuming and costly, further deterring adoption.
- Perceived Complexity: Some in the industry view new technology as overly complex, fearing that it might complicate rather than simplify their work processes. This perception can hinder efforts to introduce innovative solutions.
Despite these challenges, there are encouraging signs that the industry is beginning to embrace technology more fully. New professionals entering the field are typically more tech-savvy and open to adopting new tools. The increasing pressure to complete projects faster, more efficiently, and within tighter budgets is driving more companies to explore and implement new technology into their workflows.
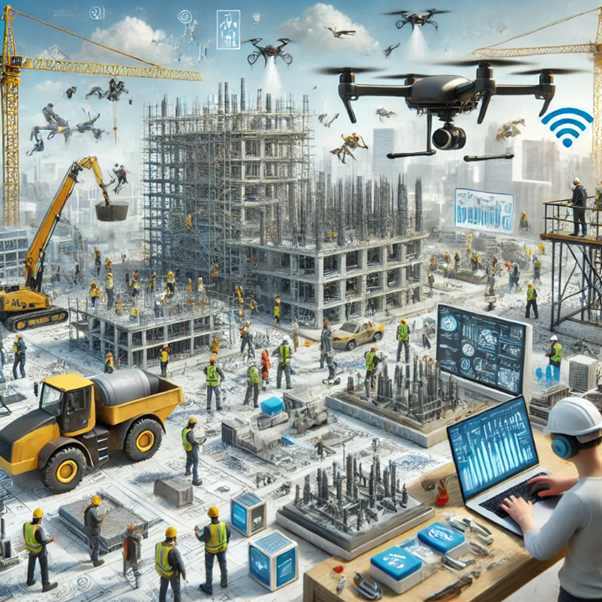
To accelerate this adoption, it's crucial to focus on education and awareness. Demonstrating the tangible benefits of different construction methods —such as improved accuracy, reduced errors, and enhanced collaboration—can help build a stronger case for investment. Moreover, developing user-friendly, scalable, and customizable solutions will make it easier for companies to integrate new technology into their workflows.
Lets take each of the factors and look at how KOPE solves these problems – its why I joined this team of brainiacs.
- Resistance to Change: This doesn’t need to be an either/or scenario. Change is completely relative, KOPE doesn’t replace your ERP or your secret sauce estimating sheet, it gets you through your traditional tendering process faster – much faster.
- Training and Adaptation: In the traditional sense of the word, KOPE needs no training. You give it a model; you tell it which building systems you want to place products on and KOPE does the rest. The placement, the optimization, the math, the QTO, the drawings – all automated.
- Cost Concerns: The KOPE license model is not user based. You can have as many users as you like, in fact, the more users, the greater the increase in your bottom line. KOPE gives you the ability to tender more work and understand which projects you might not want to win too!
- Integration Issues: There are none. Rather than choosing traditional design or detailing tools to connect with, KOPE takes an IFC, meaning you can use your choice of authoring tool, the outputs of KOPE are the same, IFC, DWG & CSV!
- Lack of Customization: You don't pick KOPE up off the shelf and have to shoehorn its features into your workflow – We onboard you and code your product information and placement rules for you – its all included. When you add new products or need design changes, we can update them for you!
- Perceived Complexity: We do the opposite, we take what can be complex calculations, multiple tools and a vast amount of re-work and automate it using the most basic level of detail.
I have been deeply involved in this space for ten years, I remain excited about the future. The construction industry has the potential to transform dramatically with the right technological tools. While the pace of adoption may currently lag innovation, ongoing efforts to address the barriers will ultimately lead to a more technologically advanced and efficient industry.
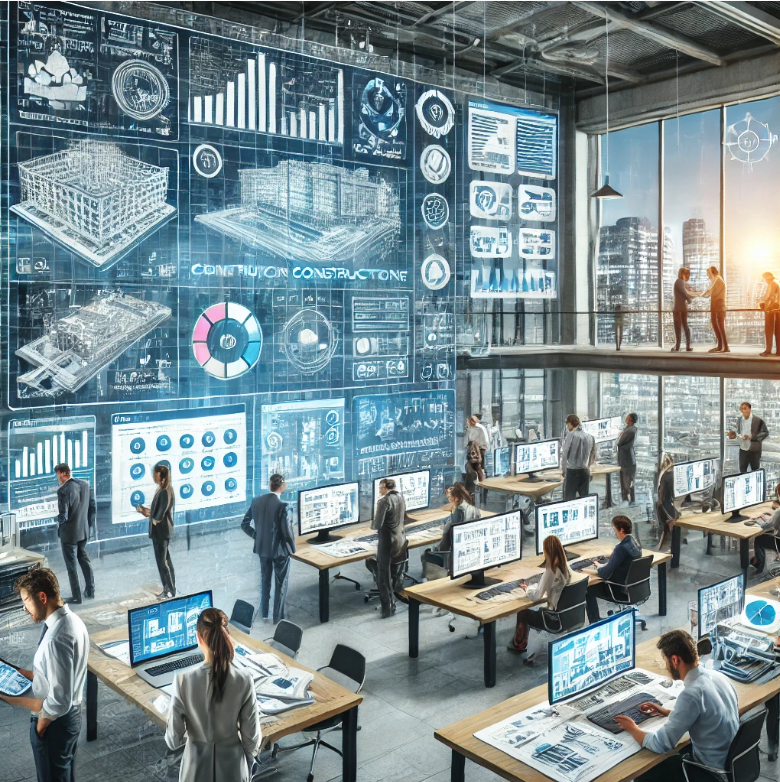