Intro
The construction industry is known to run projects in silos, each as a bespoke solution, which is then made difficult to deliver on time and budget with typically small profit margins, worsened by the lack of visibility and long-term demand. This has meant that organisations responsible for delivering projects have lacked confidence to invest in innovations, standardisation and adoption of digital technologies.
The Playbook part 2
The Construction Playbook states that the UK government will ‘’look to procure construction projects based on product platforms’’ and outlines an intent to ‘’harmonise, digitise and rationalise demand’’ to ’’accelerate the development and use of platform approaches, standard products and components, to transform the market’s ability to plan, invest and deliver digital and offsite manufacturing technologies’’.
There is much talk on ‘product platforms’, ‘digital twins’ and ‘digital libraries’ as being pivotal to the success of ‘the golden thread’.
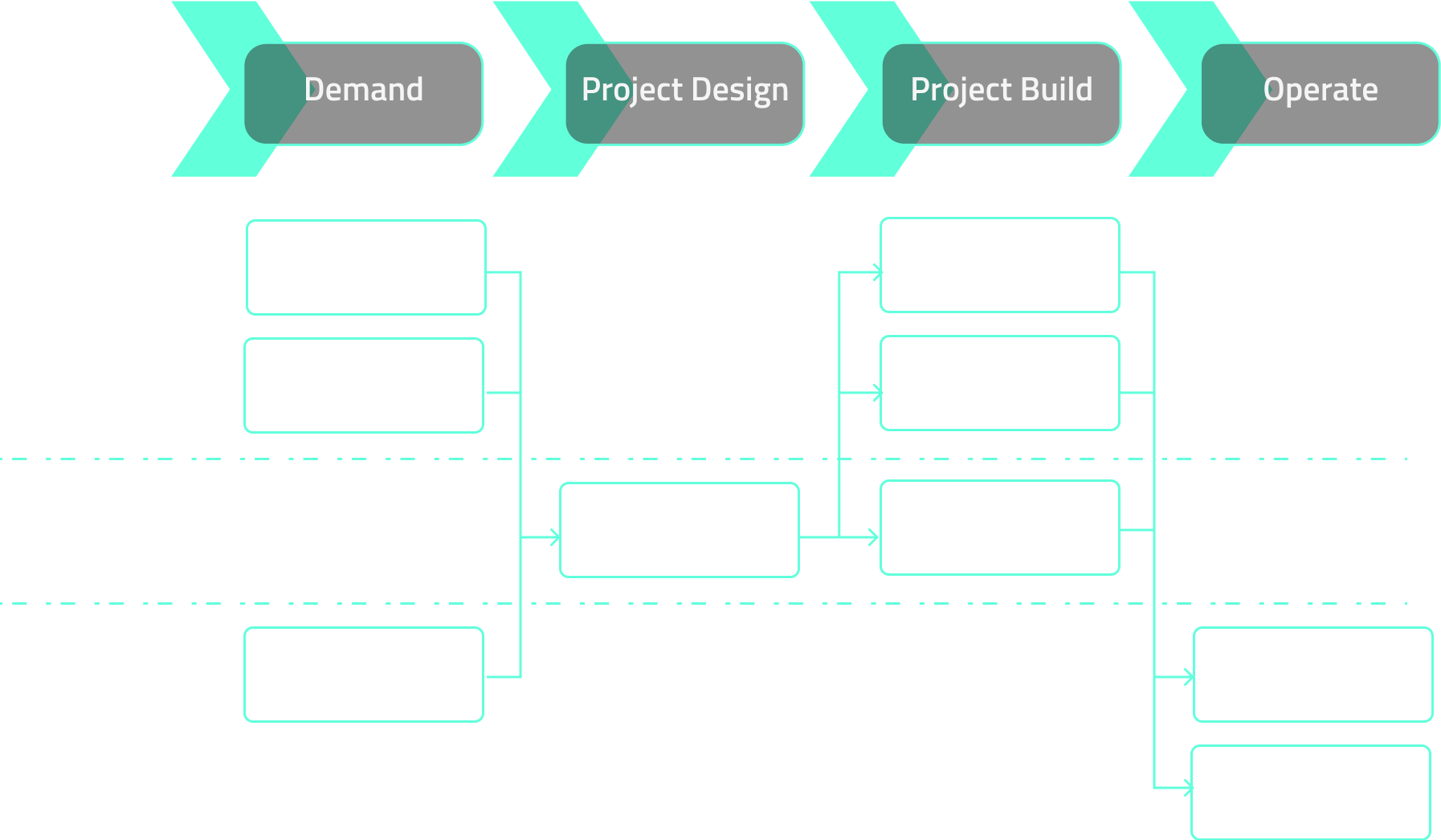
The ‘Golden Thread’ is a phrase we are all very familiar with as the government and many other industry bodies recognise and promote the need for digital technologies to develop and enable the creation, collation, management and exchange of information in the entire life-cycle of a built asset, and the digital twin is considered the access point to carry it.
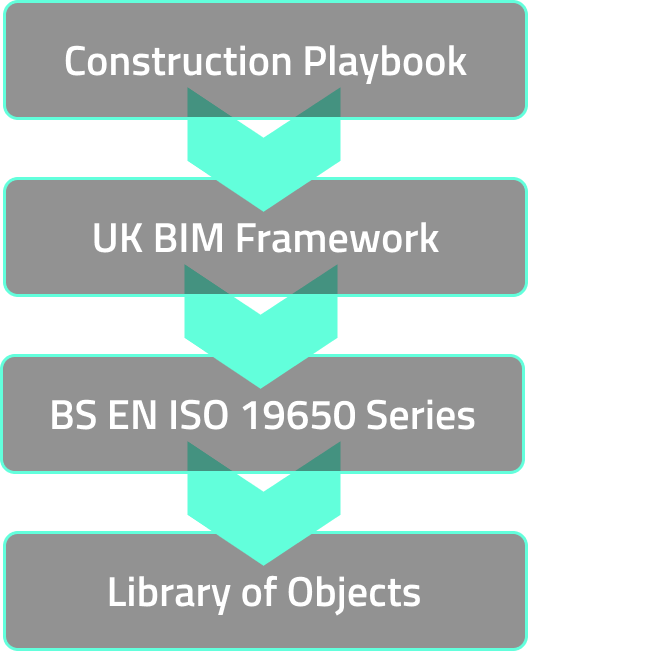
There is ample guidance, initiatives and standards out there on how we can better link information between products and projects, but still we lack the visibility and funding to invest in the technology that can enable it.
Standardising repeatable elements, whether that is physical products, specifications or processes, is critical to the success of the offsite industry. A standardised supply chain can work well together with digital technologies to systematically create and manage product information and translate that into something that is both human and machine readable. Systems follow a set of rules, and rules can be automated to gain efficiencies and reduce cost, increase margins and improve quality.
We at KOPE have developed a digital platform for the offsite industry with two key aspects that can support and enable the deployment of product platforms. KOPE will digitise the supply chains geometrical properties, analytical attributes and system logic. The structuring of the information and activities allows suppliers to control the exposure of information in the MMC Market, and the ‘Project Domain’ to access, explore and deploy at any point along a project timeline within KOPE.
.png)
Below we have outlined the steps we are taking in the development of KOPE to create a software platform that facilitates and enables the deployment of product platforms. We have mapped them against the 8 rules set out in The Product Platform Rulebook.
Deployable:
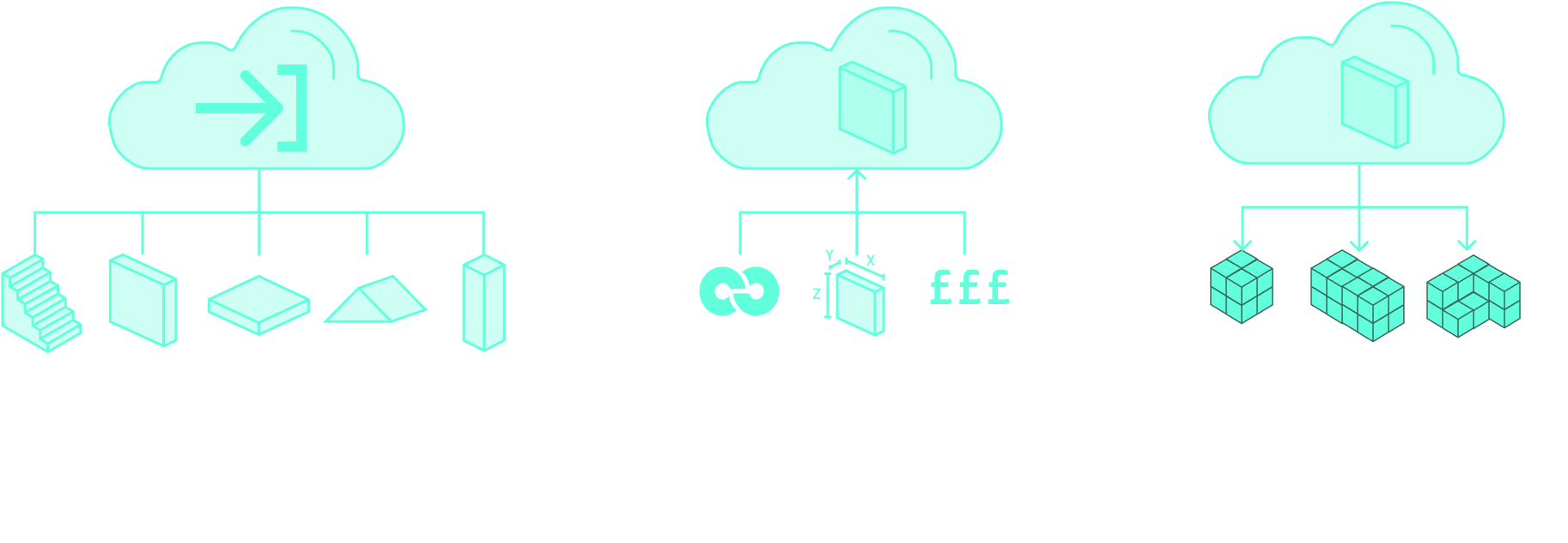
The MMC Market forms an industry wide database that has been designed to provide visibility and access to our real world supply chain. It allows suppliers to upload and host products that carry geometrical, analytical and technical information alongside it’s systematic logic required in its application. Because this information is hosted at product level, KOPE can consume this product data, uploaded by the ‘Product Domain’ suppliers, and then enable the ‘Project Domain’ to instantly apply them to multiple projects.
Configurable:
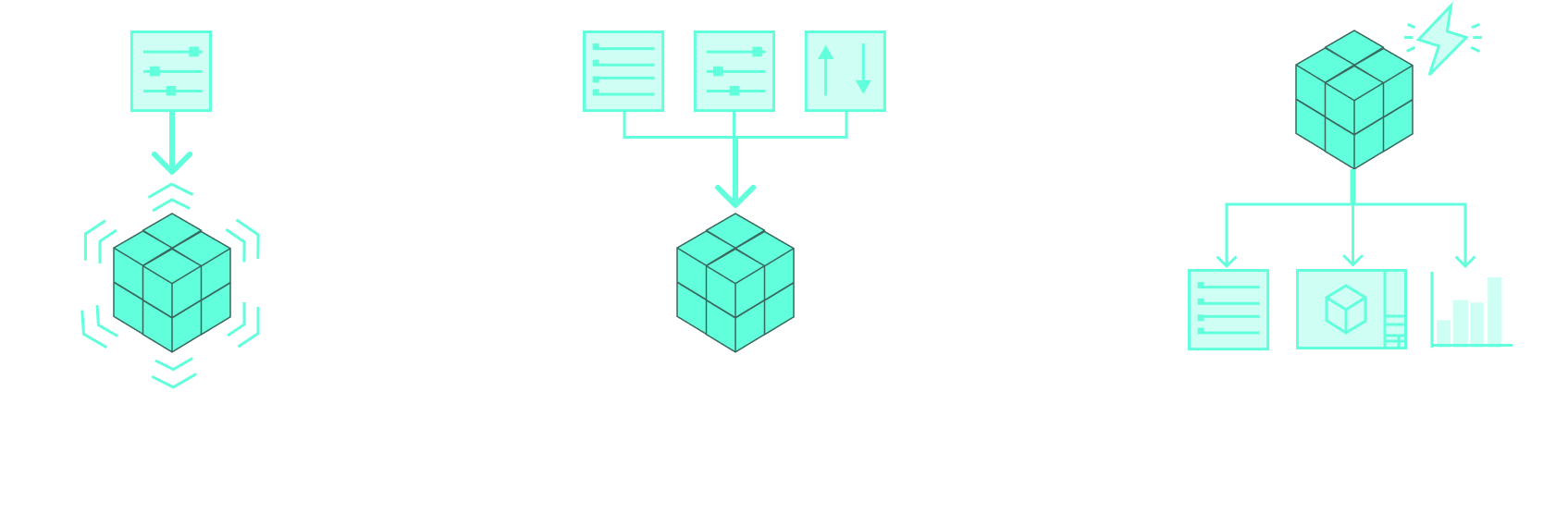
Many construction products are based on a designed system, meaning the product data is not just fixed geometrical variables, but also systematic logic that can be applied to a number of solutions. A wall panel system for example can come in a number of dimensions within upper and lower limits, but the build-up and performance might be fixed.
The MMC Market gives the ‘Project Domain’ the ability to flex and explore products, outside of the project design environment. It allows the user to quickly identify the products attributes and limitations set by the supplier, such as incremental fixed dimensions. It’s objective is to provide support in developing project solutions and improving knowledge on how the products and systems work and how it might impact the constructability and feasibility of our projects. From here you are able to bring a product into KOPE for application. The embedded product data forms the input into the configurator in KOPE. KOPE will automatically convert the design file into your chosen real world products, by generating and placing product elements based on those rules and support the generation of optimal designs. KOPE can optimise the placement by allowing the ‘Project Domain’ to filter and prioritise data values such as cost, waste and quantities and request the ranked solutions that satisfy requirements. Once the optimum solution is identified, KOPE will automate outputs instantly, such as drawings, quantities and coordinate files.
Common Repeatable Elements:
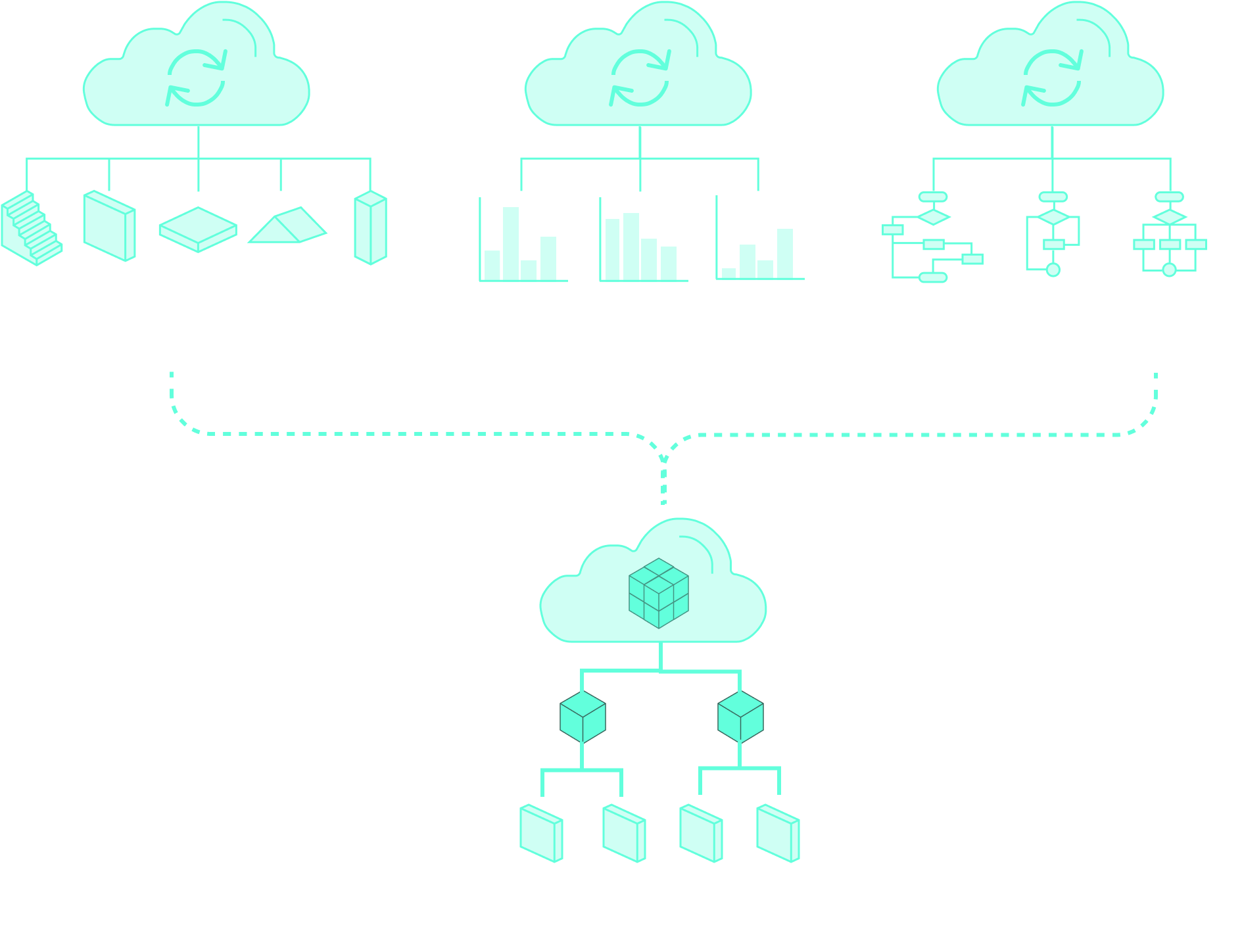
MMC Market is a free and searchable database of offsite products however, it is not just a digital library of repeatable geometrical objects.
KOPE digitises all of the attributes and repeatable processes that the supplier defines, enabling suppliers to have control over the application of their products into any project. This is not a revit family which can be edited by the user once it has been downloaded from the internet. KOPE instantly applies the product to a project design file, and will only expose the permissible variations determined by the supplier assuring consistency which is required in order to scale and gain value from efficiencies.
Interfaces:
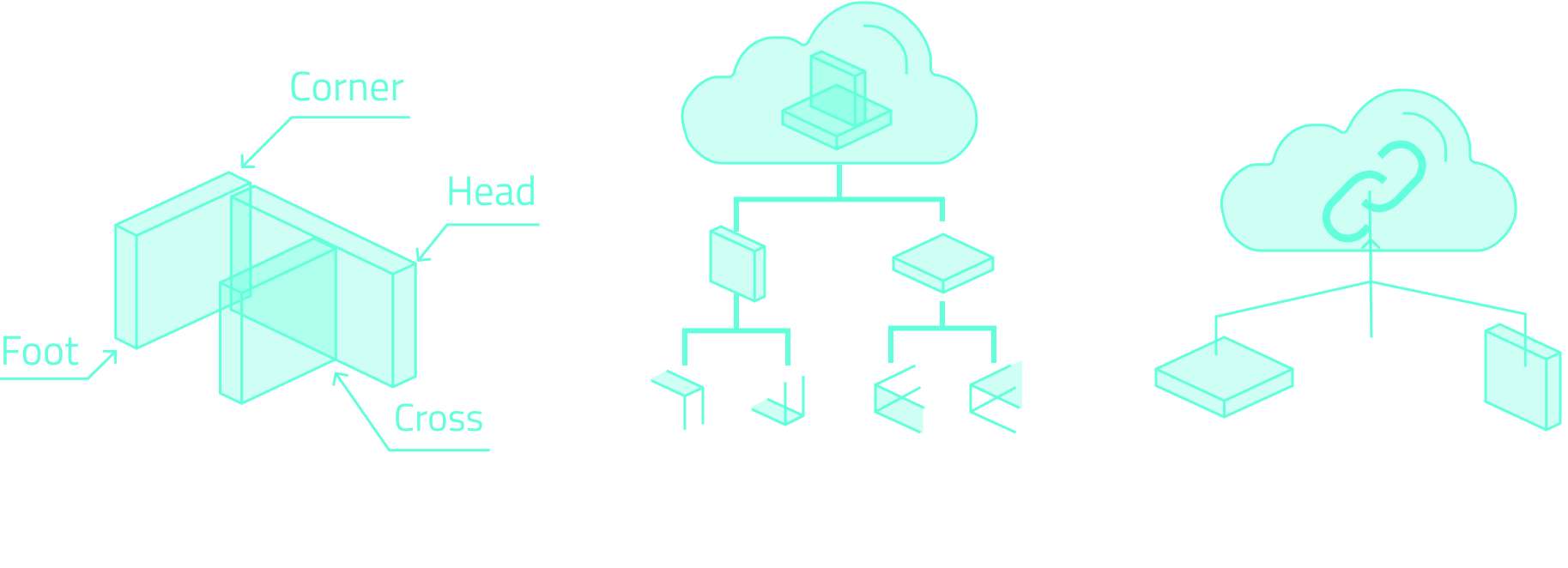
The Independent Review of Building Regulations and Fire Safety (Hackitt Report) and subsequent Building Safety Act has set the requirements for clear and transparent testing regimes particularly around product performance assessments as part of a system and not individual products.
KOPE takes a definition and data management approach. It will structure data entry points to prompt suppliers to specify and define various standard interfaces when adding their products to the digital platform. This will, in turn, support early engagement and help highlight any interdependencies with other specialist suppliers by facilitating the identification of standard interfaces. The suppliers can maintain their own library of products and can add details around interfaces and their core requirements, it will also enable them to update any changes, add test data etc. The suppliers can also link their products to projects that have successfully integrated with other building elements and products.
Quality:
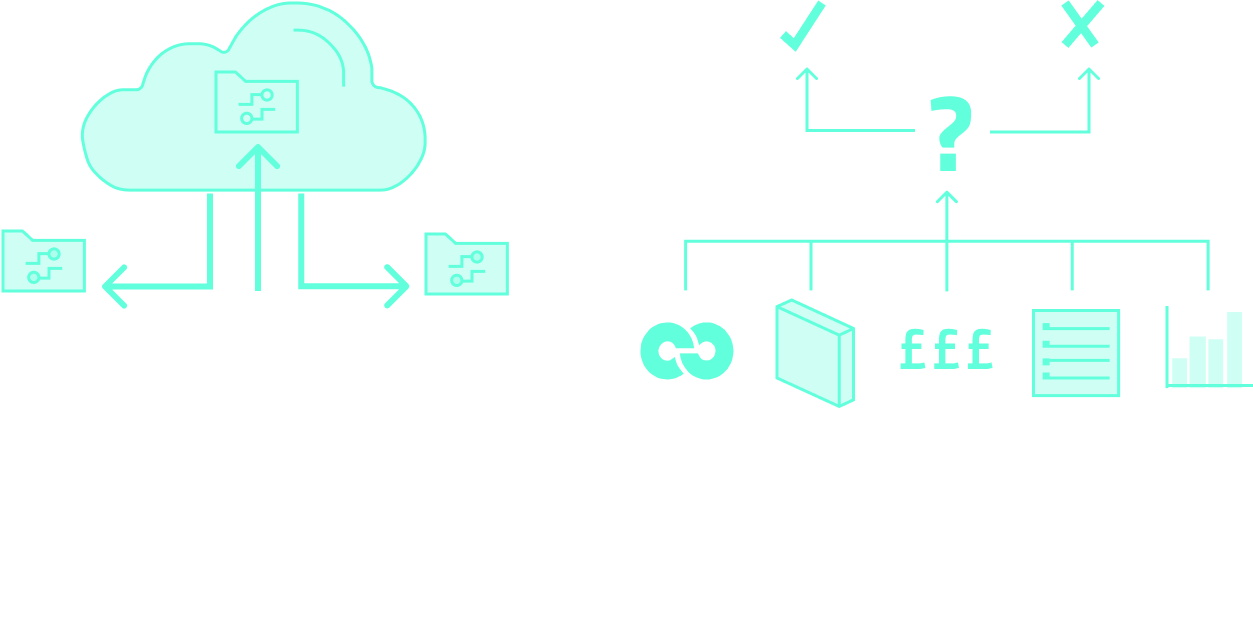
There are two challenges in both the product and ‘Project Domains’ with verification between project requirements and compliance, which has historically led to higher costs, delays and poor quality. KOPE provides live metrics on the product solutions when applied to projects, such as placement, types, locations, logistics etc which enables a quick appraisal against the project requirements. It can also connect this to cost per X given by the supplier.
Typically a digital library is stored project to project and relies on the project members to manage and maintain it throughout the project lifecycle. Whereas with KOPE, the product database is managed by the supplier in a supplier portal and is then made public, giving them the control and certainty that the product is utilised correctly and efficiently. The supplier can manage the product content to ensure its definition is accurate, up to date and ready for deployment into projects. This will allow for the products to be updated considering lessons learnt during its application.
Structured Information:
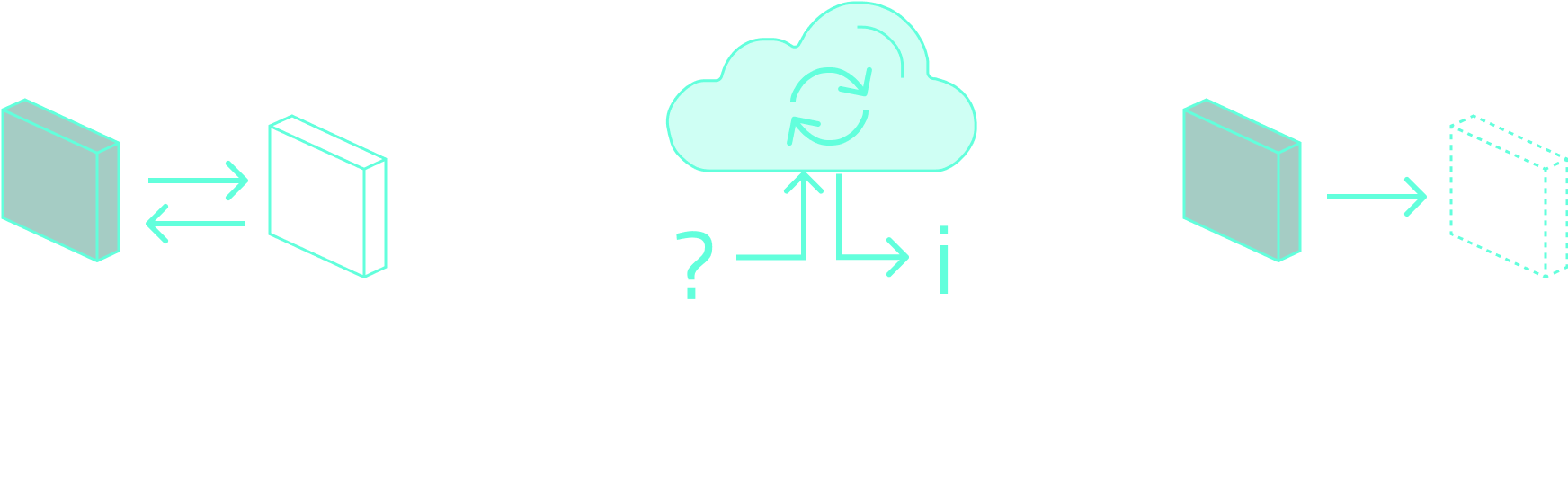
The construction industry is very fragmented, worsened by the way in which information is managed within the ‘Project Domain’. A large portion of the industry, particularly product supply chains, use pdf’s which are typically shared via email or downloaded from a website. The result is siloed information that is not standardised, making it difficult to compare and transfer products and projects and support aggregated demand.
“the development and use of consistent, structure, rules and language …. to facilitate a shared understanding”.
The BIM framework and BS 8541-1 calls for object libraries to format product information in a way that enables the easy transfer of information between individuals and products in the project itself, but what does this mean and how can we facilitate that consistently across the industry?
KOPE’s is a platform that structures data entry in a clear and consistent way to create a common framework across products, projects and organisations. The defined structure enables the ‘Product Domain’ to easily upload and update product information in a simple and effective way. It also allows the product supplier to expose only the information that is wanted and needed. KOPE will give you live metrics across multiple solutions for exploration and enables the user to filter and appraise options for comparative and verification activities facilitating informed decision-making and to help develop clear performance based outcomes. It also allows the ‘Project Domain’ to quickly iterate and compare products.
Open:
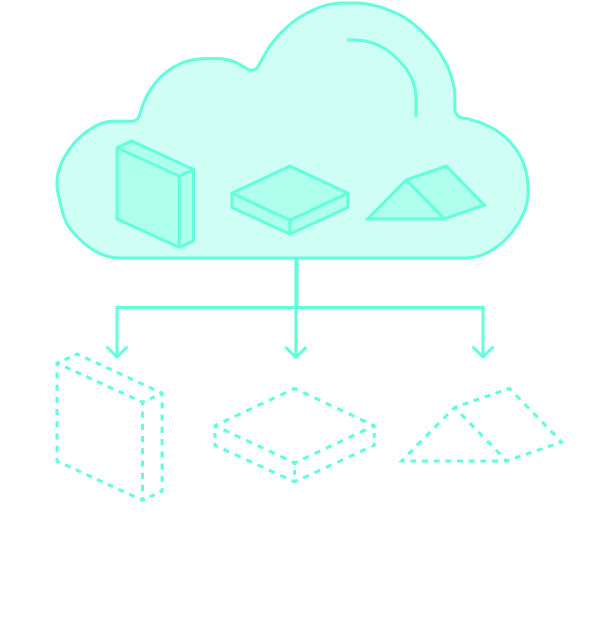
‘’engaging early with the supply chain and developing clear, appropriate outcome-based specifications are critical factors in achieving timely and costly effective delivery.’’
The MMC Market is already breaking ground in providing a platform for product suppliers and offsite consultants to market themselves and their products for free. It supports visibility to our real-world supply chain by consolidating, structuring and linking products within the market and allowing free access to search, filter and compare. Users can gain useful insights into the organisations and projects to form a greater understanding of successful implementations and business credibility. It allows the ‘Product Domain’ and ‘Project Domains’ to connect for effective collaboration earlier on reducing downstream issues.
KOPE facilitates a consistent foundation that utilises IFC to users to upload and download throughout the project phases to support external processes and integrate directly around existing tools.
Circular:
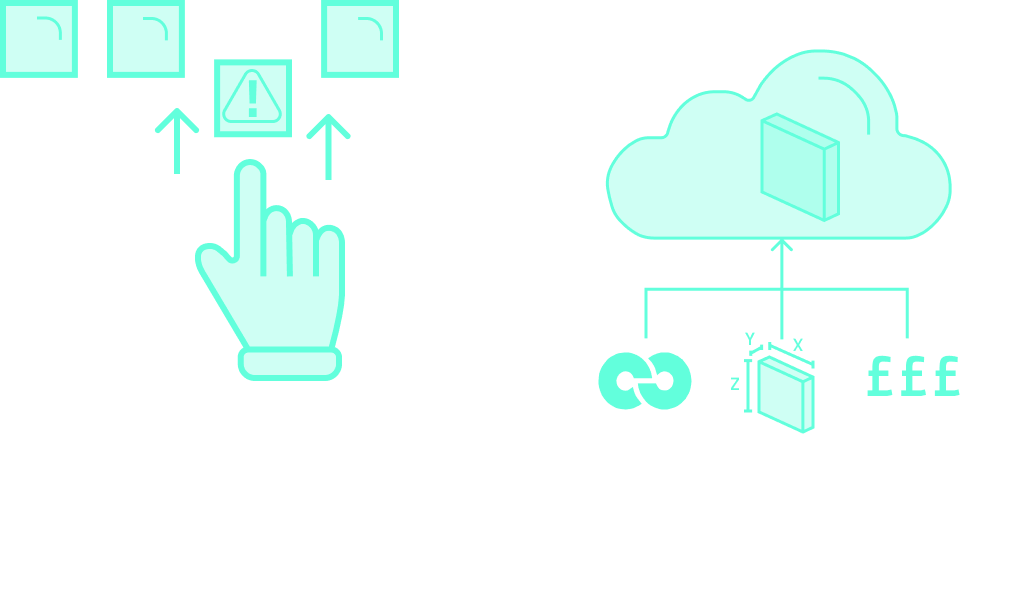
KOPE and MMC Market facilitates a consistent approach with the structuring of information for organisations, projects and products which enables interoperability. It provides suppliers with the ability to control data, including the identification of evidence of the circularity of products with detailed information on maintenance, re-use and end of use are indicated and attached to the product.
Conclusion
The Product Platform Rulebook has had a positive reaction as it promotes standardising of design, process, components and interfaces to improve the quality, speed and safety of the industry. But this is only made possible through the structuring of data and there has been many attempts at providing guidance.
We need to enable product and system innovation. There are a number of digital technologies out there but they lack focus on offsite construction and its inherent technical requirements. We need to provide a ‘product first’ platform that supports the requirements laid out in the Product Platform Rulebook.
‘’Changes on this scale will only take place if the whole industry works together. On the industry-side, we need to share the vision and consistently apply the principles across all members. The whole sector has an opportunity and a role.’’ Construction Playbook. Sep 2022.
We at KOPE are creating a platform to support those who innovate with their products and projects, creating a standard framework to enable suppliers to easily manage their products, and to enable designers to apply their products early on, influencing design and ensuring constructability.