In the ever-changing landscape of UK construction, over the past year, we've observed some fantastic offsite projects that aim to redefine the way we build, focusing on sustainability, efficiency, and quality.
From a Football stadium to Europe’s tallest modular tower to a low-carbon hospital building and a ‘kit of parts’ office, let’s take a look through some of the highlights...
Overcoming Engineering Challenges with Everton Stadium
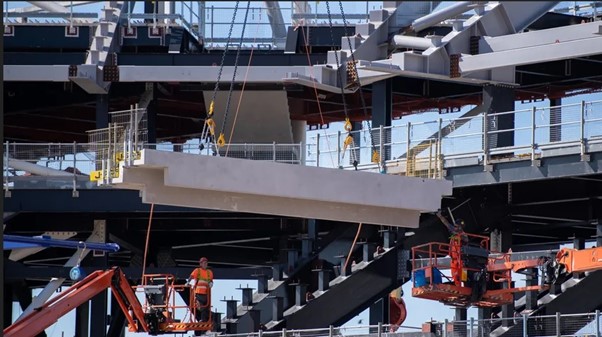
Navigating the challenges of a dockland location, Everton FC's £500M Bramley-Moore Dock stadium is emerging as a testament to innovative design and construction methodologies. Laing O'Rourke, the main contractor, and North Yorkshire's Severfield, responsible for fabricating the steelwork, have embraced modern methods of construction to overcome the engineering complexities of this unique setting.
Facing the Mersey River, wastewater treatment works, a main road, and a disused dock, the site presented considerable challenges. Laing O'Rourke, employing advanced digital design and modern construction methods, utilizing various tools to develop a 3D model of around 6,000 components, to address potential issues before construction began.
Comprising steel and precast concrete, the stadium's superstructure is a great example of offsite construction, with precast concrete components forming floors, walls, supporting columns, and terraces. All these were manufactured at Laing O’Rourke’s Centre of Excellence for Modern Construction, including precast composite red brick façade panels.
The meticulous planning of materials deliveries and the use of preassembled components not only enhance quality control but also contribute to a more efficient construction process and material usage.
With precast elements and steel components arriving on-site, the stadium, seating 53,000, is on track for completion in 2024. Everton FC's Bramley-Moore Dock stadium not only promises to be an iconic sporting venue but also exemplifies the transformative potential of offsite construction in challenging locations.
Europe's Tallest Modular Building in Croydon
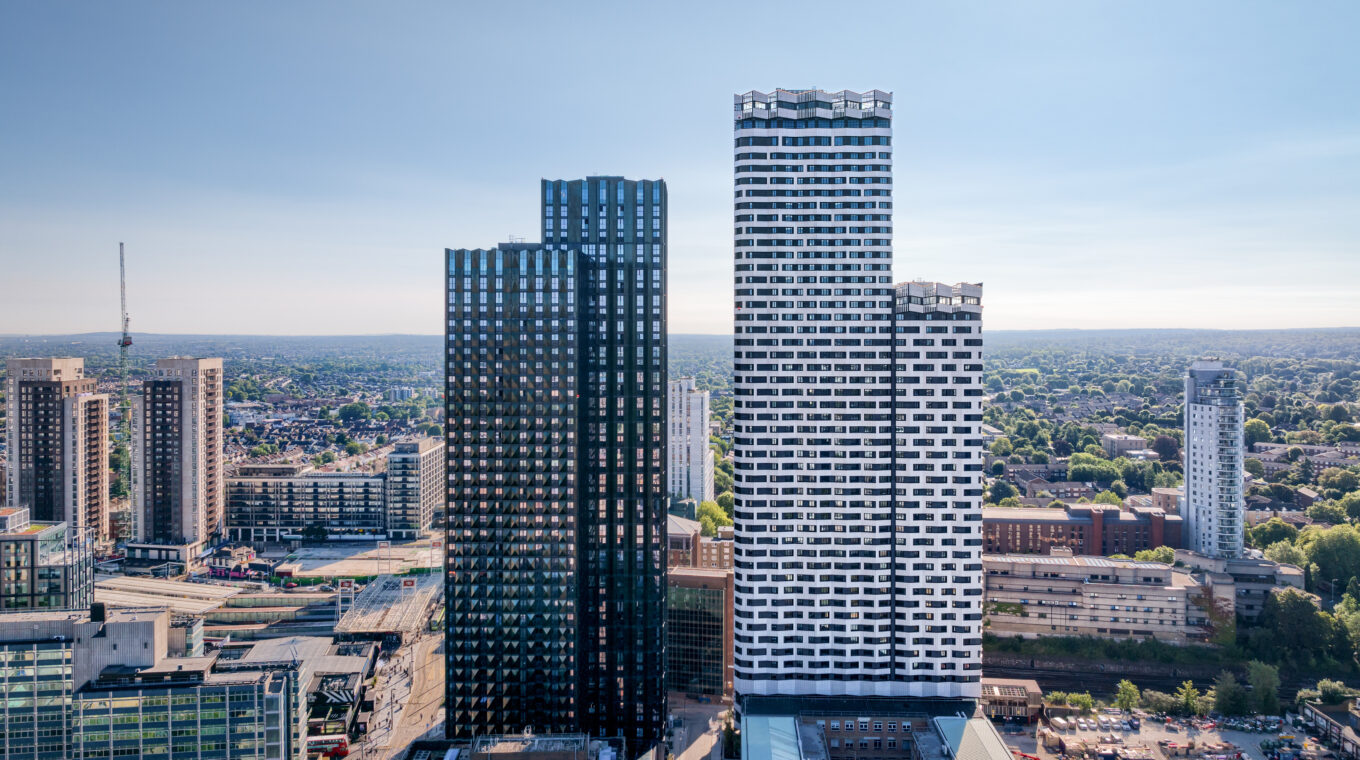
Standing at 163 meters, College Road is Europe's tallest modular building in Croydon, south London. Completed in October last year, the College Road development, designed by HTA Design and executed by volumetric developer Tide, consists of two towers—a 50-story and a 35-story structure—wrapped in a pleated ceramic facade.
This build-to-rent scheme accommodates 817 one-bed and studio apartments, including 120 affordable homes in the smaller tower.
The tower stands just across the street from the 135-metre-tall Ten Degrees building, also designed by HTA, which, at the time of completion in 2020, claimed the title of the world’s tallest modular housing scheme.
Notably, 1,725 volumetric modular units dropped into position around a concrete core in just 40 weeks as part of a 28-month total construction program, two months ahead of schedule, showcasing the efficiency of offsite solutions provided by Vision Modular Systems.
Approximately 73% of the development floor plate was installed in just 32% of the overall timeline. Contrary to the assumption that offsite construction leads to uninspired design, the building's striking facade draws inspiration from geometric patterns prevalent in south London's architecture from the 1950s and 60s, in particular the brutalist No.1 Croydon, also known as the '50p building’ by Richard Seifert.
Groundbreaking hospital
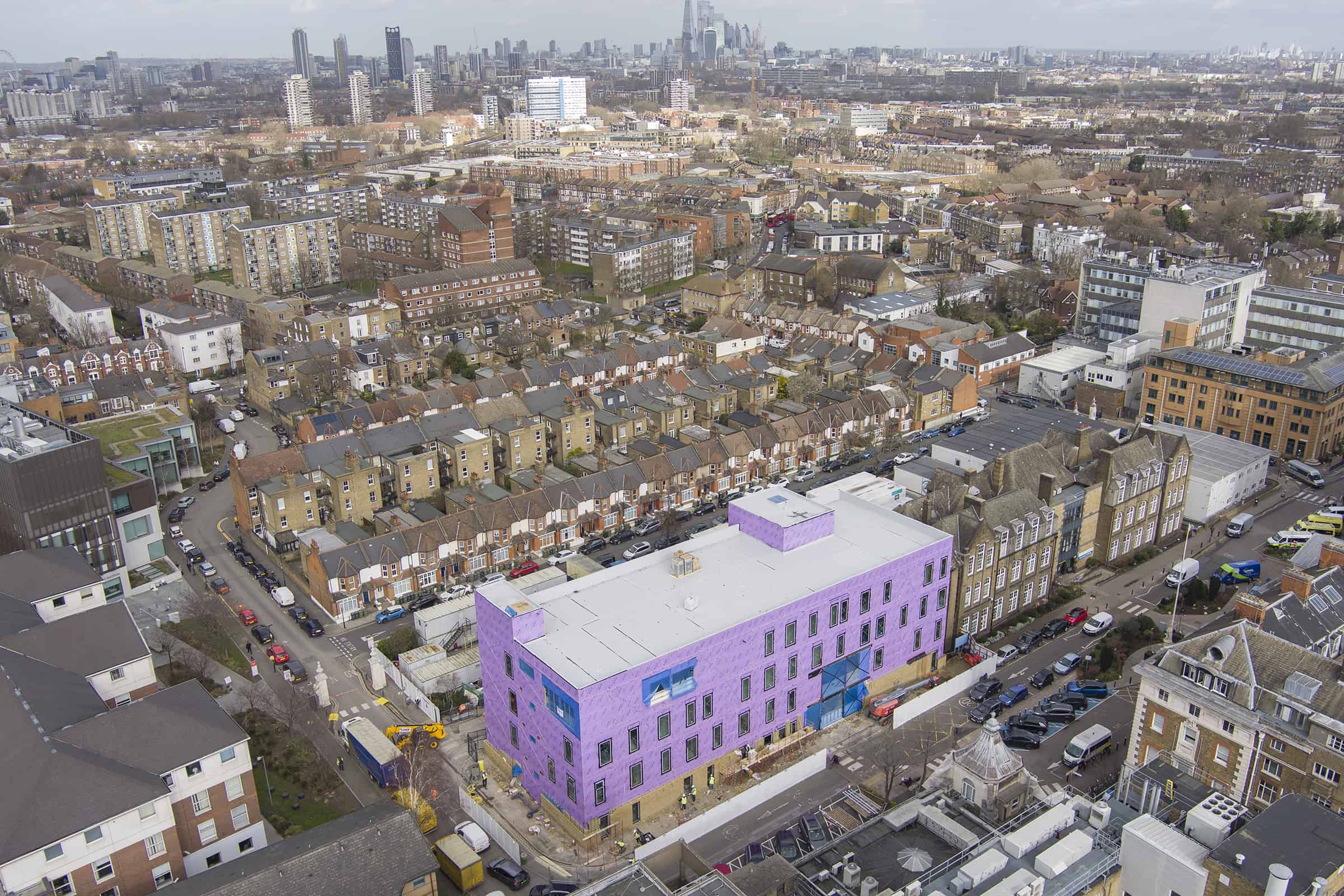
In another significant achievement, King's College Hospital saw the completion of the NHS's largest-ever offsite modular scheme this spring. Premier Modular delivered a four-story, 3,450 sqm outpatient services building that seamlessly integrates with the existing hospital.
The facility, featuring 48 consultation rooms and eight procedure rooms for various medical services, stands as an example of the potential of offsite construction in healthcare.
The fast-tracked nine-month build program, from concept to completion, demonstrated efficiency, with coordinated cranes installing 132 steel-framed modules in just 23 days. The process was designed to ensure minimal disruption to the existing hospital site, including the helipad and air ambulance helicopters.
Utilizing a combination of low-carbon measures and renewable energy sources, the outpatient building features quality insulation, an energy-efficient heating and cooling system with heat recovery, and an efficient radiant panel system powered by air source heat pumps.
The design, developed in collaboration with clinicians and patient representatives, surpasses energy efficiency targets, aligning with the London Plan and new SAP 10 carbon factors.
First ‘kit of parts’ office block
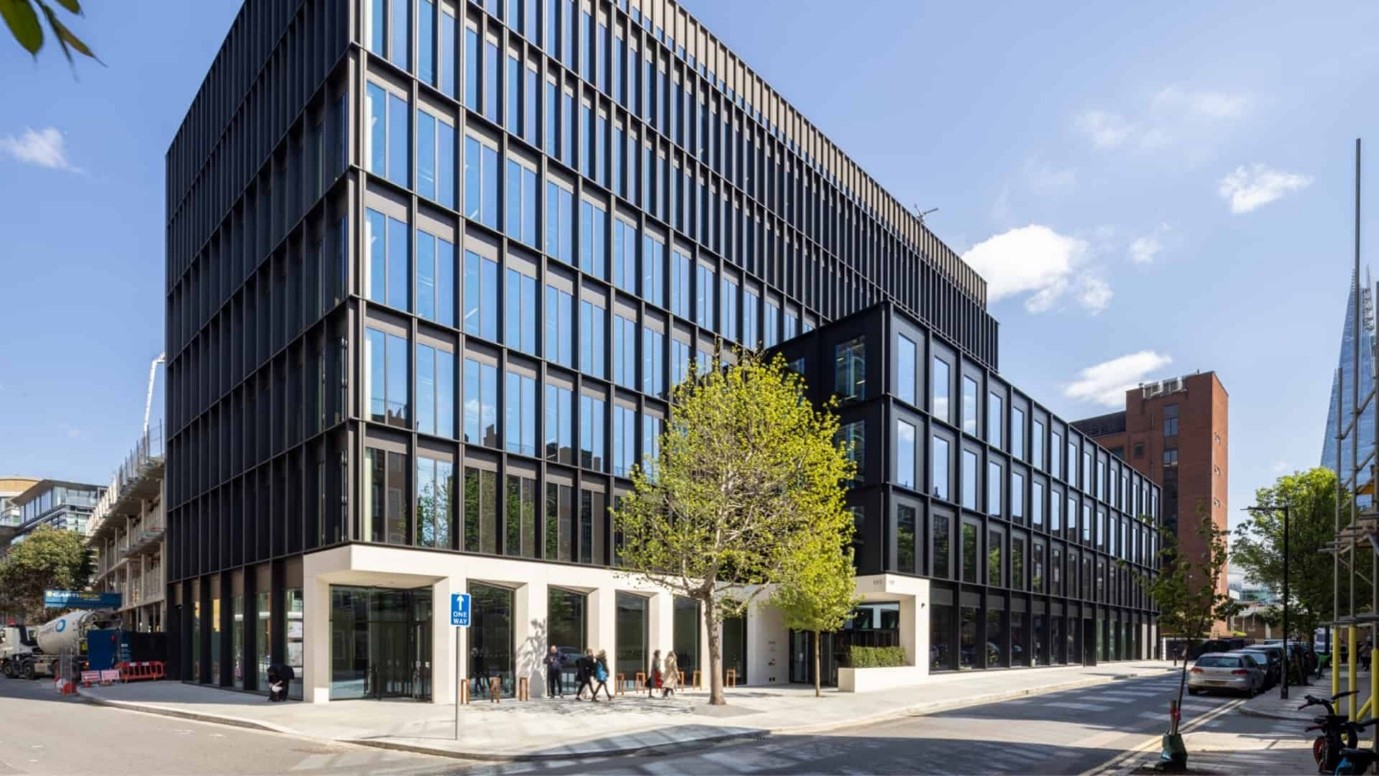
March 2023 marked the completion of the Forge office development, a pioneering project for Landsec in Southwark, London. This 139,000 sq ft venture, consisting of two 9-story office buildings behind Tate Modern, stands out as the first-ever private sector building employing a ‘kit of parts’-led solution centered around a Platform Design for Manufacturing and Assembly (P-DfMA) structural frame.
Executed by NG Bailey and multi-disciplinary design consultants Bryden Wood, this project leveraged NG Bailey’s specialized offsite manufacturing facility in Bradford. The structural frame embraced common, repeatable components tailored to fit a standard 9m x 9m office grid. This approach empowered supply chain partners, particularly in M&E and façade, to develop complementary platform elements, enhancing consistency and productivity.
Functioning as a prototype, the building served as a learning exercise. Analysis by the University of Cambridge identified promising targets for future platform adoption, including a potential 25%-55% reduction in superstructure construction time and a 40% reduction in façade installation time. The use of cassette M&E modules showed potential program improvements of 66%-90% compared to traditional installation methods.
The Forge stands as Landsec’s inaugural net-zero commercial office building, adhering to the UK Green Building Council’s Net Zero Carbon Buildings Framework. The platform approach played a pivotal role in emissions reduction, aligning with ‘lean manufacturing’ principles by minimizing material usage, opting for the lowest carbon materials, and fostering circularity and reusability. Reversible bolted connections facilitate the easy removal and reuse of steel components within the building.
The Forge has been recognized with numerous awards for its innovative approach and sustainable design. As we celebrate this success, it underscores the importance of pushing these boundaries further. The industry needs more projects to adopt a similar approach across sectors, driving progress and setting new standards for efficiency and sustainability.
This brief rundown of projects gives an inspiring snapshot of the current state of MMC in the UK; stay posted for a concise rundown of what we can expect from the sector in 2024…