Intro
The game-changing benefits of modular construction - faster completion, safer manufacturing, better quality control, and lower environmental impacts - are maximised in high-rise buildings where an efficient geometric form and a large number of standardised and repeatable modules ramp up economies of scale. Given the housing crisis in the UK, speed and volume of delivery are particularly important and towers provide more homes per square foot than any other housing solution.
Recent advances in MMC structural systems, new design codes and contractors’ growing experience with the technology have driven a surge in modular high-rise development worldwide and many of the tallest buildings, either completed, underway or planned, are located in the UK.
Reaching for the skies demands a robust structure and modular high-rises are typically supported on stacks of steel or concrete modules, which each have their own advantages and disadvantages. For example, steel modules are around 20% to 35% lighter than concrete and provide more flexibility in architectural design, thanks to an open space framing system and larger module sizes, but they tend to have lower fire resistance and sound and thermal insulation.
Load bearing wall modules are most common in concrete buildings, used to transfer gravity loads to the foundation and resist lateral loads. Conversely, corner-supported steel modules transfer gravity loads to the slab, then to edge beams and corner columns and into the foundations. Lateral loads are resisted using separately braced frames or a reinforced concrete core.
Record breakers
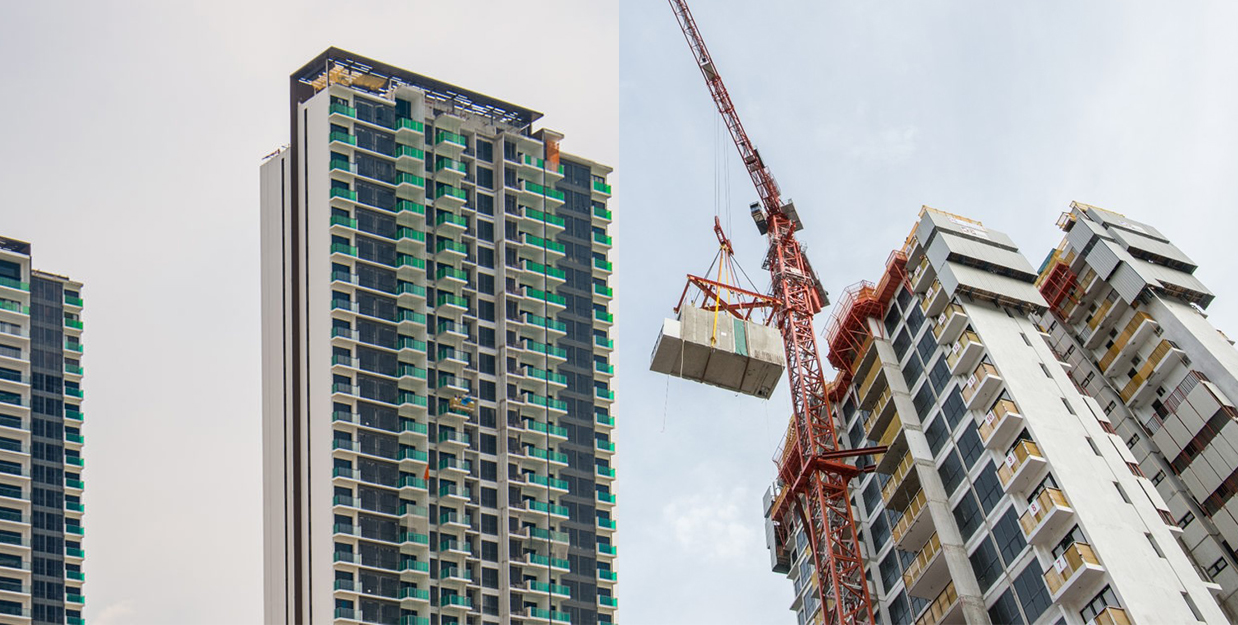
What’s widely acknowledged as the world’s tallest modular building is Clement Canopy in Singapore, a pair of 140m-high towers made from prefabricated concrete modules.
Designed by ADDP Architects and constructed by Bouygues Bâtiment International, the scheme’s 1,899 pre-finished modules were cast in a yard in Senai, Malaysia, then fitted out to an almost finished state at a factory in Tuas, west Singapore.
Window frames, glazing, doors, wardrobes and MEP, including water and sanitary pipes, electrical conduits and ducting, and painting, were all completed before the modules arrived onsite. In a carefully choreographed sequence, the concrete core was built in tandem with the stacking and installation of modules. According to Bouygues, going modular and using a central materials and logistics platform was more sustainable, reducing waste onsite by 70% and offsite by around 30%.
Singapore has been promoting modular construction in a drive to boost productivity, having made it mandatory on selected public residential projects since 2014. Narrowly missing out on the top spot, the world’s second tallest modular building is the Ten Degrees residential high rise located in Croydon, south London.
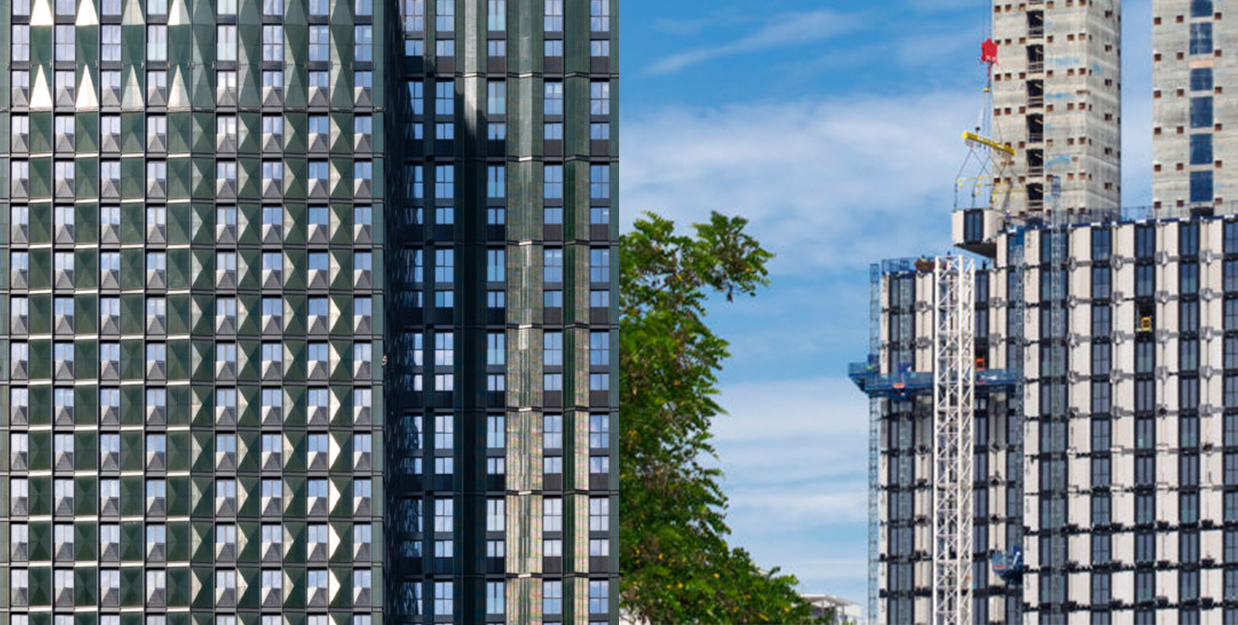
The 135m scheme at 101 George Street, close to East Croydon station, comprises two towers of 38 and 44 storeys, completed in May 2021. Designed by British architects HTA Design, it incorporates almost 1,500 modules manufactured offsite by Vision Modular Systems and built by contractor Tide Construction.
The 546 rental flats feature open-plan living spaces, floor-to-ceiling windows and Juliette balconies. Alongside an art gallery and cafe located on the ground floor, other amenities include a rooftop gym, sky lounge, co-working space, rooftop and ground-level terraces and a private dining room. The project challenges the perception that MMC puts limits on inspirational design, the multi-faceted geometric glazed terracotta facades draw on the rich heritage of local mid-century buildings including Richard Seifert’s iconic No1 Croydon to create a distinctive architectural aesthetic.
According to Simon Bayliss, managing partner at HTA Design, the entire project took just 39 months to deliver, from first concept to handover, and going the modular route resulted in a 40% reduction in embodied carbon compared to traditional construction methods, with a significant reduction in waste.
Tide claims to be behind 7 of the world’s 10 tallest modular buildings, recent projects include the 27-storey Mapleton Crescent tower in Wandsworth, south London, built for housing developer Pocket Living. Flats in this block were craned into place at an impressive rate of one storey per day. The Apex House student housing scheme in Wembley reaches to 28 storeys, and at the time of completion in 2018, was the tallest modular building in Europe.
Let’s go higher
Not satisfied with these vertigo-inducing achievements, construction teams are already pushing the boundaries of modular technology with several substantially taller buildings soon to smash existing records.
Due to complete in 2023, the twin-tower Avenue South Residences development in Singapore, designed by ADDP Architects for UOL Group and Kheng Leong Company, will reach 56 storeys and 200m high.
A focus on Prefabricated Prefinished Volumetric Construction (PPVC) will see around 80% of each module for the 1,074 apartments built offsite, in line with a Singapore Government initiative to improve construction productivity by up to 40% in terms of manpower and time savings.
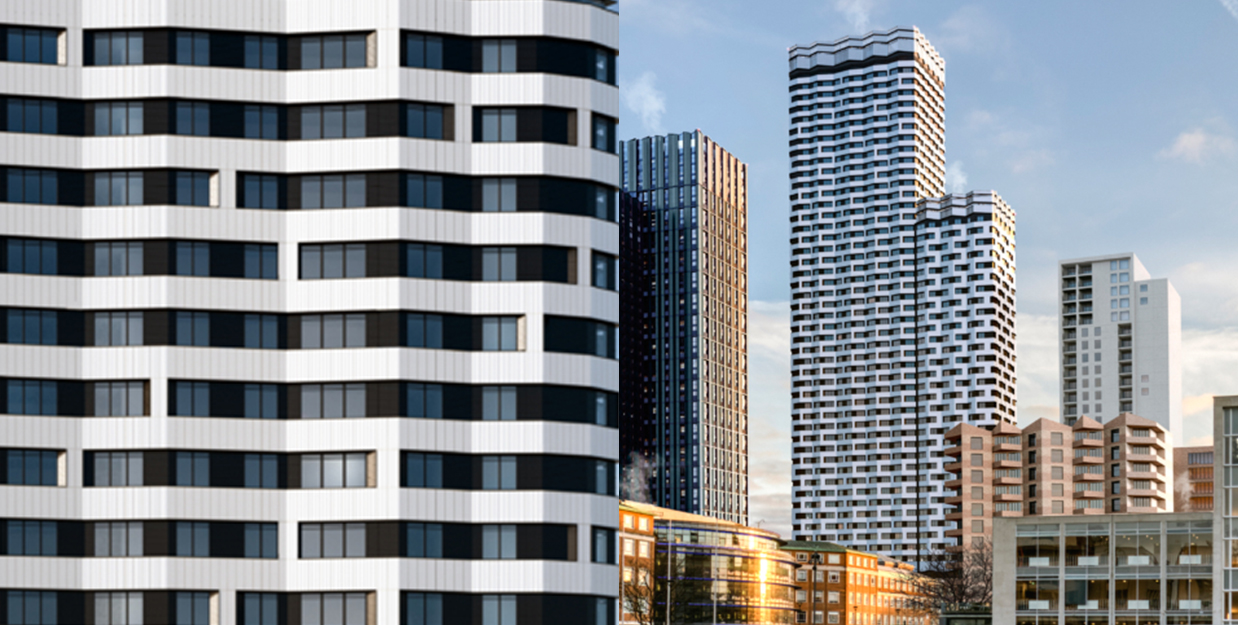
Back in the UK, Tide Construction is currently onsite delivering the College Road residential development in Croydon, which will pack 937 bedrooms and apartments into two towers standing 34 and 49 storeys tall. That’s 5 storeys higher than its previous tallest project Ten Degrees.
The contractor also has the planning thumbs up, to build a 48-storey student accommodation tower at Canary Wharf in London. Sitting amongst many of the city’s iconic high-rise buildings, the 30 Marsh Wall project, designed by EPR Architects, will reach 156m tall and provide over 1,000 beds and feature a large roof garden.
The modular approach on this scheme is expected to cut construction time by up to 50% and result in a more dependable construction program, with efficient construction logistics.
Designers and contractors working with MMC have clearly learned a thing or two about building upwards and ongoing technology investment programs, rigorous R&D and testing regimes will ensure future modular advancement over the coming years.
However, offsite high-rise construction is not without its challenges, a lack of design codes of practice and the technical complexities of those that do exist have hindered widespread adoption. Where a contractor on a traditional job can hold off mobilising and committing resources if a project stalls in planning, that’s not an option on a big modular construction job where there’s an emphasis on upfront design and adequate lead in times for offsite manufacture. A recent report by Arup identifies the opportunities that can help local planning authorities and other users of the planning system smooth the adoption of MMC.
Closing
Nevertheless, modular is clearly the future, offering a robust solution to many of the challenges faced by the construction industry, including the housing crisis, the climate crisis and skill shortages, also helping deliver on targets around sustainability, safety, scalability and minimising disruption to local communities. In other words, it can lift us even higher…