MMC
Faced with a chronic housing shortage, a ‘levelling up’ agenda and pressing net zero targets, the UK government is putting its weight behind offsite construction to boost productivity and efficiency. But what are the benefits and will MMC ever make it into the mainstream?
Modern methods of construction (MMC) are not new, but recent years have seen a resurgence of interest and activity in the space with innovation extending far beyond the previous focus on offsite volumetric modular manufacturing.
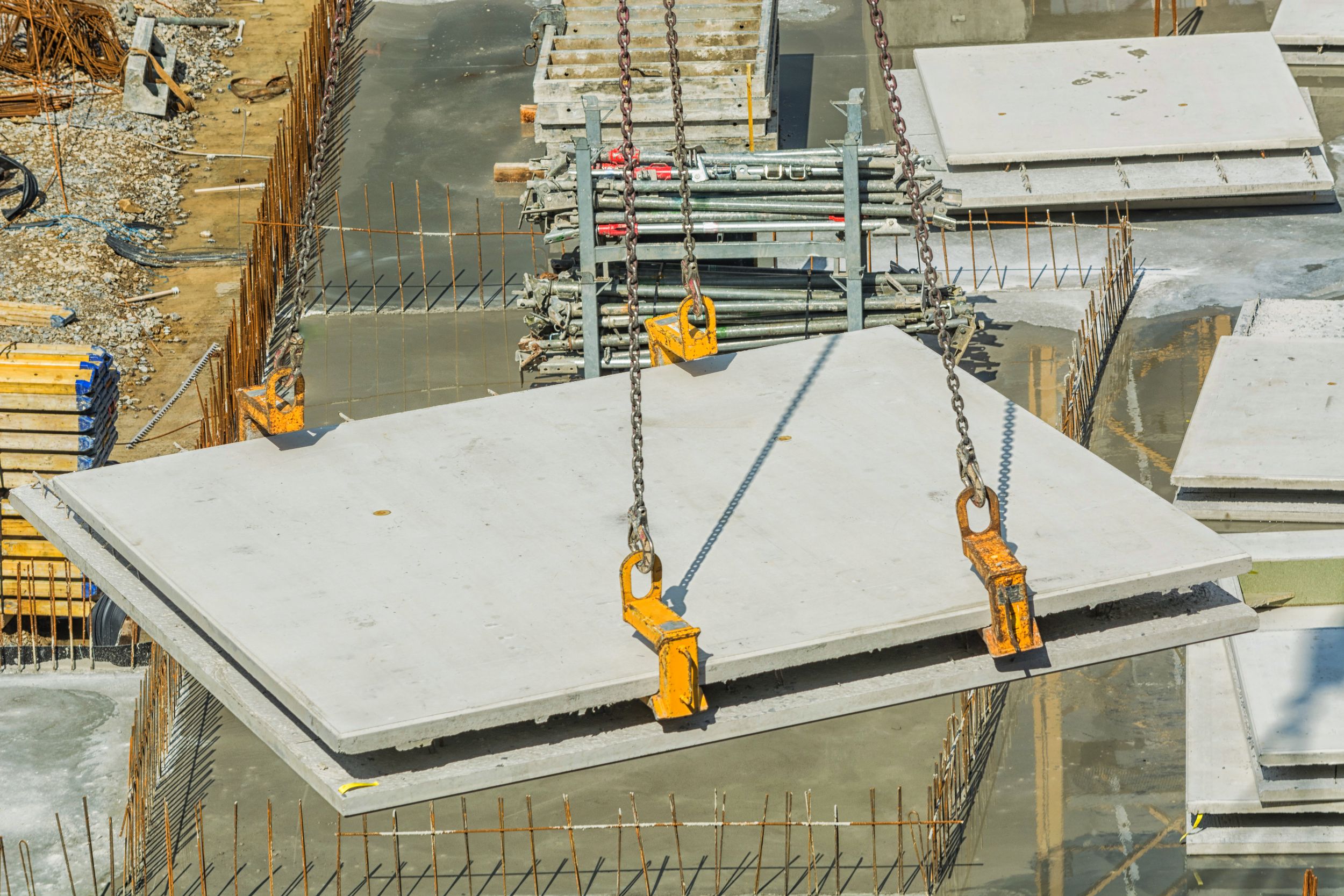
Keen to capitalise on efficiencies and benefits around productivity, quality, reduced waste and labour, the UK government has spearheaded a range of offsite programmes and policies intended to push MMC to the forefront of construction industry thinking. The direction of travel has already been set by ambitious programmes abroad. Japan first embraced MMC 50 years ago and now has the capacity to build more houses per year than the entire UK. Sweden is building at least 45% of its new homes offsite in factories and China has set a target to construct 30% of all new buildings offsite by 2026.
The UK government enshrined MMC in its long term policy with the Construction Sector Deal in 2019, which highlights the need for offsite manufacturing to help the industry deliver a 33% reduction in the cost of construction and a 50% reduction in time, from newbuild inception to completion. The policy requires government departments to adopt a presumption in favour of offsite construction across suitable capital programmes, where it represents best value for money. Building on this mandate, a major $10billion offsite construction framework, for use by all government departments, was revealed by the Crown Commercial Service at the start of 2022. Offsite techniques will also be fundamental to the £650 billion of public and private sector money assigned to UK priority infrastructure projects over the next 10 years, with Housing Authorities in particular required to commit to modular under an £11.5 billion affordable homes programme.
Of the 528 future projects, programmes and other investments included within the National Infrastructure and Construction Pipeline, 143 will make best use of MMC, ranging from digital design to offsite and volumetric construction.
Mindset shift
Offsite manufacture has never been ‘mainstream’ in the UK, yet it could help address several key issues facing society and the economy.
The UK is in the midst of a housing crisis with demand for property far outstripping supply. Whitehall has set a target to complete at least 300,000 new homes a year by the mid-2020s and MMC is considered a key vector to achieve this. Furthermore, the UK has a legal commitment to reach Net Zero greenhouse gas emissions by 2050 and prefabrication has been shown to reduce deliveries to site, meaning less pollution, a reduction in construction waste, and the opportunity to consistently build to a higher quality improving air tightness and conserving heat. The Covid-19 pandemic hit society hard and the Government’s Project Speed initiative was established by the prime minister in 2020 to help stimulate the economy by accelerating work on major infrastructure projects. Offsite manufacture has obvious relevance to its stated goal to "cut down the time it takes to develop, design and deliver vital projects.”
Beyond national drivers, the specific problems faced by the construction sector can also be addressed by a factory-based approach. Construction productivity has virtually flat-lined during the past 20 years, even though industrial productivity has risen by some 25% over the same time. MMC’s ability to streamline activities between the factory and the site and improve onsite methodologies have been shown to deliver construction time savings of between 10% and 50%.
Construction is facing a serious skills shortages, with a high percentage of workers now reaching retirement age and the dearth of skilled and unskilled trades exacerbated by the impacts of the pandemic and Brexit. A shift to offsite processes could help mitigate this occupational shortfall. According to recent research by the Construction Industry Training Board, if the government’s targeted 300,000 homes a year were met using MMC it would require 158,000 additional workers by 2025, some 37,000 fewer than the 195,000 workers required using traditional methods.
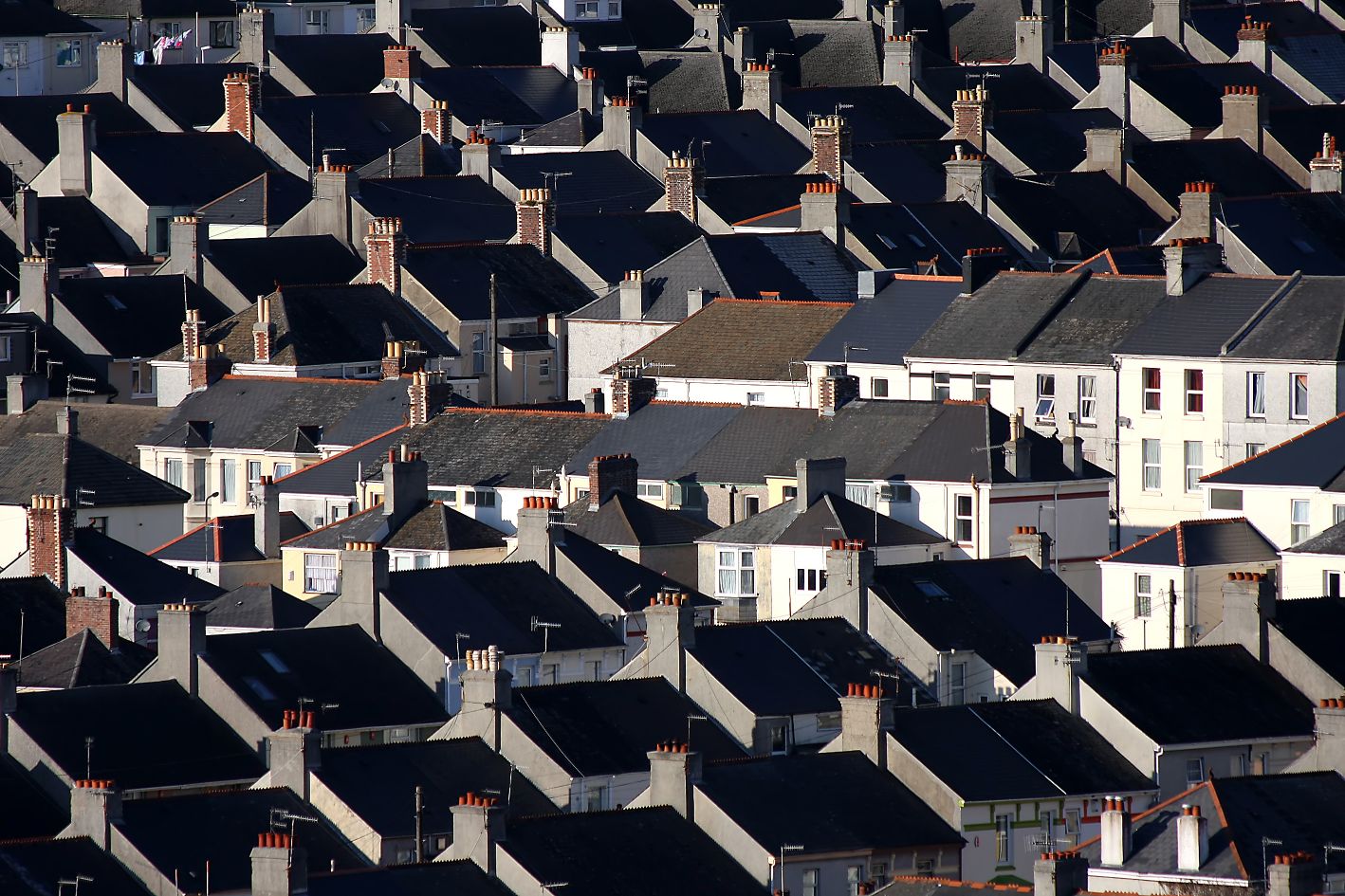
Proponents of offsite methodologies also point to benefits related to increased predictability, quality (quality control under factory conditions can reduce time spent on onsite snagging) and minimal waste compared to bespoke methods.
Digital evolution
Digital design and prefabrication go hand in hand and the recent rejuvenation of interest in MMC is synonymous with the drive to digitise construction. Government support for offsite closely parallels its support for Building Information Modelling, having mandated the approach on all publicly-procured projects in 2016. BIM aims to digitise all construction information and makes it possible to precision model and test in 3D all components needed to construct building elements. These can be scheduled, costed and interrogated in detail before committing to design freeze and manufacture.
Digital models can boost efficiency across the entire project lifecycle. The government understands that models and associated data can help them better manage assets and estates, driving more efficient operations and facilities management. The dynamic nature of challenges facing the sector highlights the importance of innovative construction techniques, but MMC has a long way to go to become business as usual in the UK. A recent survey carried out by Buildoffsite for construction consultancy BECG found that main contractors are still behind the curve in the adoption of offsite solutions, with sub-contractors making up the majority of the market. The report revealed a lack of accreditation among offsite companies, which it said “goes some way to understanding the lack of adoption on offsite, possibly because of the lack of confidence and viability as a solid construction project with robust assurance.”
Procurement routes for MMC are another concern, with over 50% of the survey respondents not on any formal sourcing platform used by public and private procurement organisations for project delivery. The Government’s new guide to procurement, the Construction Playbook published at the end of 2020, encourages the adoption of MMC for faster delivery of projects and at scale and could give industry the certainty it needs to invest in these unfamiliar, but potentially highly impactful technologies.
What do we mean by MMC?
The term Modern Methods of Construction has become all-encompassing, in an effort to improve understanding the government recently created a definition framework, which divides MMC into seven distinct areas:
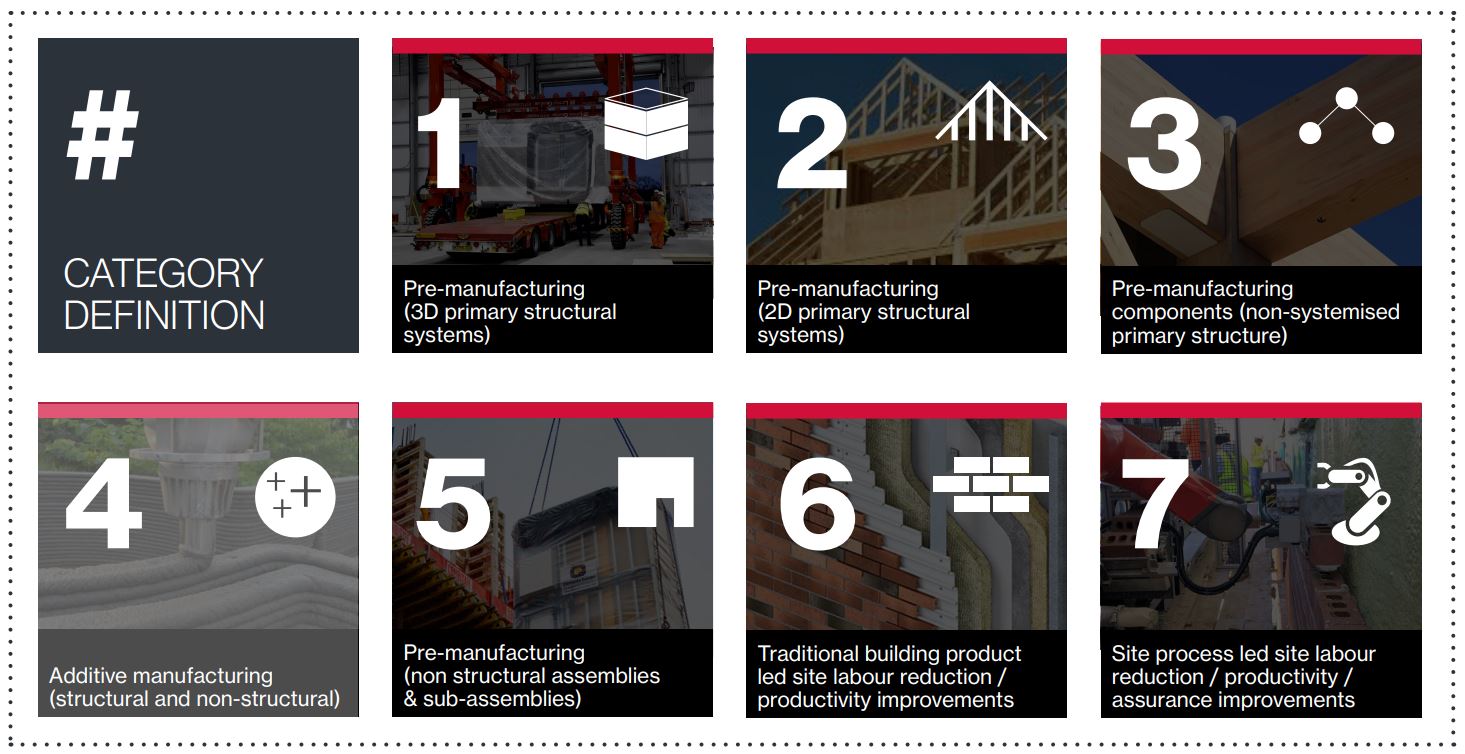
- Pre-manufactured 3D primary structural systems - volumetric units that either form the entire structure or are podded into rooms integrated into another building method.
- Pre-manufactured 2D primary structural systems - flat open frames or closed panel systems assembled onsite to create a 3D structure.
- Pre-manufactured components - beams, columns, wall structures and slabs that are not part of a systemised design.
- Additive manufacturing - 3D printed structural or non-structural components based on digital design.
- Pre-manufactured non-structural assemblies and sub-assemblies - this includes volumetric podded assemblies and panelised assemblies such as floor and roof cassettes.
- Traditional building process improvements - Such as using large-format walling or roofing.
- Site process-led labour reductions - Such as BIM, autonomous plant, robotics, augmented reality, or digital site verification.
With KOPE, we believe there is a need for a purpose-built software to help accelerate the adoption of offsite construction. We will be at the forefront of this change within the industry, helping to foster a more sustainable and repeatable construction industry.